All published articles of this journal are available on ScienceDirect.
Advanced Technologies of Potash Fertiliser Production from Promising Raw Materials
Abstract
Aims
To propose a new method for producing ballast-free potash fertilisers from promising raw materials.
Background
Potash ores from Chelkar and Zhilyan deposits with huge reserves were not previously explored. In this study, promising previously unexplored potash ore deposits with huge reserves were examined. Chemical and mineralogical compositions of potassium rock from Chelkar and Zhilyan deposits were determined based on which carnallite nature of both salts was found. However, Chelkar salt also contains a large amount of impurities of sodium chloride and calcium sulphate, and Zhilyan salt is more concentrated in potassium, contains less halite and does not contain insoluble gypsum. For these salts, a method of incomplete dissolution for raw material enrichment in potassium was selected and validated. The process of subsequent processing of the enriched salt was investigated by means of nitric acid decomposition of this salt and two-stage crystallisation of target salts from the extract. Thermodynamic probability of the reactions’ occurrence confirms the formation of an equilibrium solution. We calculated the activation energy for the main reaction,which proves the inside-kinetic region of behavior.
Objective
To study kinetics and chemical equilibrium of nitric acid decomposition of potassium raw materials.
Methods
Processing of previously unexplored potash ores, IR, XRD, SEM, and spectrometric methods of analysis.
Results
Chemical and mineralogical compositions of potash rock from Chelkar and Zhilyan deposits were determined, and the main stages of their processing have been studied.
Conclusion
New effective methods for producing chlorine-free potassium and potassium-nitrogen fertilisers have been proposed, which are characterized by minimal water input and the absence of production waste. As a result, a method for producing ballast-free potash fertiliser was proposed, which was not previously used for other kinds of raw materials. This method allows us to not only enrich raw materials with the potash component, but also to separate an insoluble gypsum intergrown with other potash minerals in the ore composition. The use of traditional processing methods does not allow for obtaining a completely water-soluble fertiliser.
1. INTRODUCTION
Everyone knows that the world population is growing steadily. The United Nations predicts that by 2050, about 10 billion people will live on Earth. To provide a growing population with food, it is necessary to increase agricultural production. Agriculture faces ongoing challenges to promote environmentally sustainable development and increase yields while arable land is limited. In this regard, the use of mineral fertilisers is a basis for ensuring food security of countries; accordingly, the demand for mineral fertilisers is constantly growing [1]. The application of potash fertilisers along with phosphorus and nitrogen ones is a necessary condition for sustainable crop yields and serves as one of the main indicators of agricultural development in each country. In the global mineral fertilizer market, potassium salt consumption has been steadily increasing for several decades. The potash fertiliser market is notable for being the most consolidated in the world due to maximum concentration of potash deposits by country. The largest producers of potash fertilisers are Canada (Nutrien holding (Saskatchewan region), Russia (Uralkali) and Belarus (Belaruskali), which account for more than 70% of world exports [2, 3]. In 2021, 46.64 million tonnes of fertilisers, or 13.55 million tonnes in terms of K2O, were produced in Canada, of which 39.6 million tonnes were produced as potassium chloride. Russia and Belarus produced 10.7 and 7.5 million tonnes, respectively, in terms of K2O in 2021. Among Central Asia countries, Uzbekistan is the main potassium salt producer of 197 thousand tons, and Uzbekistan’s share in world production is 0.5% [4].
Application of chloride-type potassium fertilisers slows down plants’ growth and development, and sodium chloride present in sylvinite significantly worsens the composition of soils, especially chernozem, chestnut and solonetz soils. In this regard, potassium sulphate has a greater advantage as chlorine-free fertiliser, applicable to all types of soils for growing valuable chlorophobic crops, which is also not hygroscopic. In addition, potassium sulphate contains another nutrient – sulphur in water-soluble form. At the same time, the share of potassium sulphate produced in the global potash fertilizer market is only 1%. A complex fertiliser, potassium magnesia, containing potassium and magnesium sulphates, is produced in even smaller quantities [5, 6].
There is no domestic production of potash fertilisers in Kazakhstan, despite the presence of a unique raw material base in earth reserves. Back in the 1960s, geological exploration work began on potash ore deposits, but so far not a single mine has been developed. According to published data, the country's subsoils store more than 8 billion tonnes of potassium salts, which are represented by the largest deposits of Satimola, Zhilyanskoye (Zhilyan) and Chelkar [7].
The reserves of these ores are among the largest in the world (Table 1), but their development has not reached the production stage [8-10].
The explored Chelkar deposit is the largest carnallite basin that has not yet been studied. Results of geological exploration work revealed only limited information about the geological structure of the main layers of the Chelkar uplift salt mass. This deposit is quite complex in structure, containing several minerals [8, 9]. Drilling wells uncovered industrial layers of potassium-magnesium salts with associated boron mineralization in salt rocks of the Permian age. The deposit is located about 160 kilometers north of another deposit – Satimola - and covers an area of about 779 square kilometers. They explored ore reserves at the Chelkar deposit amounting to more than 1 billion tonnes [11, 12].
Deposit | Location | Field Area, Sq km | Tons (billion) | Mineralization |
---|---|---|---|---|
Zhilyan | Aktobe region | 88 | 1.1 | Sylvinite Polyhalite Halite |
Chelkar | Uralsk region | 779 | 1.2 | Carnallite Halite |
Satimola | Akzhayik district | 246 | 6.5 | Sylvinite Polyhalite Borate |
The Zhilyan deposit is located in the southwestern part of the Aktobe Urals region. The forecast reserves of potassium salts are estimated at 1 billion tons. Polyhalite rocks consist mainly of polyhalite (65%) and halite (27%) with minor admixtures of sylvinite, anhydrite, kieserite and calcite. The production zone of the Satimola deposit is distinguished by the presence of boron-bearing layers separated by rock salt in addition to potassium-magnesium layers. The largest explored ore reserves amount to more than 6 billion tonnes [7, 13]; however, its industrial development has not yet begun.
Potassium chloride separation from carnallite is much more difficult and expensive than from sylvinite, due to the need to separate a quaternary system. In this regard, potassium chloride production from carnallite has not been developed at existing potash enterprises processing sylvinite ores [14]. With huge resources of natural potassium and potassium-magnesium salts, only chloride salts are processed, and a small volume of carnallite salts from the Verkhnekamsk deposit (Russia) is processed into metallic magnesium [15-17]. Natural potassium ores predominantly contain impurities of anhydrite and halite, and during the mineral-salt separation, NaCl almost completely passes into a product, contaminating it. In solutions with low magnesium chloride content, sodium chloride solubility is significantly higher than that of potassium and magnesium chlorides. This circumstance can be used to study the possibility of preliminary enrichment of natural potash ore [14].
There are various methods for producing potassium sulphate and chloride from natural sulphate type potash ores. Conversion based on potassium chloride interaction with a sulphate containing reagent is a promising method for producing potassium sulphate [15-17]. In Germany, Congo, Brazil, Argentina, and Israel, these ores are processed into potassium chloride and complex compounds. In the USA and Great Britain, a technology for processing polyhalite salts to produce potassium sulphate is being developed [18].
As a solution, scientists have studied processes for removing halite from Iranian carnallite or separating sylvinite by reverse flotation with alkylmorpholines as a collector. Under optimal flotation conditions using a flotation machine, a 90% extraction rate is achieved [19, 20]. There is also a known method for producing potassium sulphate from polyhalite ore by halite washing with water, calcining and leaching the polyhalite, followed by separating the gypsum from the solution via filtration [21]. The disadvantage of this method is the complex two-stage process of washing polyhalite, which does not completely remove chloride and significantly reduces the degree of extraction of potassium sulphate.
Researchers have also studied the process of washing polyhalite ore from Zhilyan and Sharlyk deposits and proposed methods for processing polyhalite through decomposition using various acids to produce nitrogen potassium-magnesium fertilizer [22-24].
However, this method does not allow to completely wash polyhalite from sodium chloride and obtain pure potassium sulphate. The authors [23] found that the maximum achievable degree of potassium ions leaching from the ore is only 80%, and 70% for magnesium ions. A review of scientific publications did not reveal any other information about the results of studying the Chelkar deposit carnallite ore, its enrichment and processing. The research of proven natural salts’ composition and search for suitable alternative methods for their processing will create a scientific basis for new productions of potash fertilisers from raw materials, the composition of which differs significantly from traditional natural potassium salts. In the presence of huge proven reserves of this raw material, organizing its processing is impossible due to poor knowledge of such a deposit and the need to use new methods to remove ballast components from carnallite ore in order to obtain water-soluble potash fertiliser.
2. MATERIALS AND METHODS
The monolithic cores were taken from the potash ore warehouse of Batys Potassium National Corporation in Aktobe city. To accomplish the main tasks set in the study, chemical and instrumental methods of research and analysis were used. To wash the ore from sodium salts, the incomplete dissolution method was used, in which crushed raw materials are washed with water taken in an amount insufficient to dissolve potassium chloride, but sufficient to dissolve sodium salts for a certain time [14]. The scheme of salt enrichment is shown in Fig. (1). The method is based on the treatment of milled ore with water, used in a limited quantity to exclude the dissolution of potassium and magnesium salts. The process parameters are shown in Fig. (1). At the end of the process, the suspension was separated into liquid and solid phases via simple filtration through a paper filter. For double washing mode, the separated filtrate is used for washing the ore twice, first with the first filtrate and then with water (shown in the scheme as 3. Washing). Both components were then analysed for the content of potassium and sodium oxides.
The content of calcium, magnesium, sulphate and chloride ions was determined using standard chemical methods. The order of reactions was determined using the Van't Hoff method. Reaction rates were calculated using the method of graphic differentiation by constructing tangents to the C=f(τ) graph. The suspension created as a result of the nitric acid decomposition was separated by vacuum filtration under 0.06 MPa. Crystallisation of potassium-magnesium salts from the nitric acid extract was carried out by means of the isothermal method at a temperature of 75°C, i.e., partial evaporation of the solution to half the volume according to the calculation of this process using the solubility diagram in the K2SO4-MgSO4-H2O system.
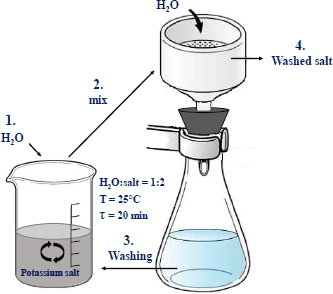
Scheme of potash salt enrichment.
Potassium and sodium content in raw materials and processed products was determined using Quant-2 atomic absorption spectrometer, as well as the PFA-378 flame photometric analyser. IR spectroscopic examination of ore samples was carried out using Shimadzu IR-Prestige IR-Fourier spectrometer 21 (Japan) with a Miracle attenuated total internal reflection attachment from Pike Technologies in the range of 400–1300 cm-1. X-ray identification was carried out on DRON-3 stationary installation with Cu-Kα radiation. Semi-quantitative XRD analysis of solid phase samples was carried out using the D8 AdvanceBruker apparatus (Germany). The processing of obtained diffraction pattern data and calculation of interplanar distances were carried out using the EVA software. For microscopic spectral analysis of raw materials and products, a scanning electron microscope (SEM) JEOL JSM-6490LV (Japan) was used. The thermodynamic probability of the occurrence of reactions was studied using the HSC-6.0 Chemistry software package (metallurgical company “Outocumpu”, Finland).
3. RESULTS AND DISCUSSION
Chemical composition of Chelkar and Zhilyan natural salts is shown in Table 2.
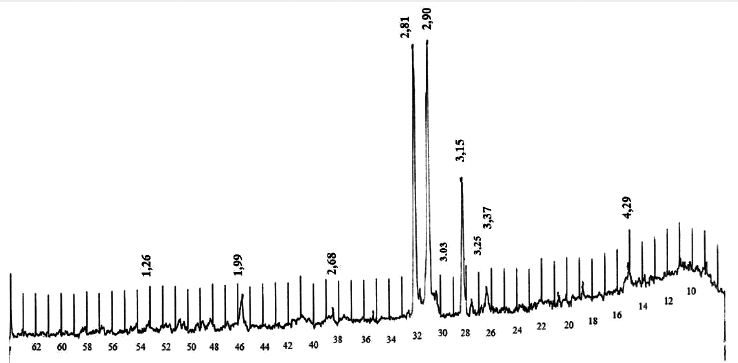
XRD pattern of potash ore from Chelkar deposit.
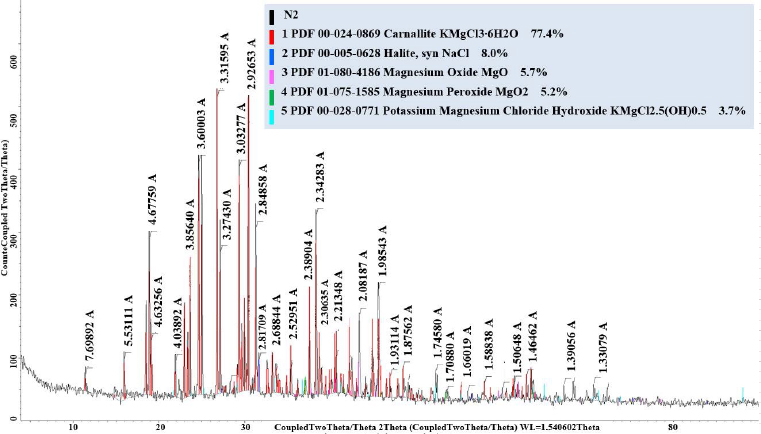
XRD pattern of potash ore from Zhilyan deposit.
Salt from Deposit | Na2O | K2O | CaO | MgO | SO42- | Cl- |
---|---|---|---|---|---|---|
Chelkar | 8.47 | 14.04 | 7.72 | 5.55 | 26.58 | 18.77 |
Zhilyan | 4.23 | 17.03 | - | 20.42 | - | 38.78 |
Сhemical composition of the Chelkar ore representative sample showed a significant presence of impurities represented by sodium and calcium compounds, in addition to the main elements of carnallite, potassium and magnesium. The chemical composition of the Zhilyan natural salt differs from the Chelkar one in its higher potassium content and absence of calcium and sulphur. X-ray diffraction studies revealed that the Chelkar salt, along with carnallite, contains lots of glaserite, halite and insoluble gypsum, whereas the Zhilyan salt is distingui-shed by its predominant carnallite content (Figs. 2, 3).
Based on these analyses, the mineralogical composition of the Chelkar and Zhilyan deposit ores was determined, which shows that potassium minerals of carnallite (33.5%) and glaserite (17.7%) predominate in the Chelkar salt composition; shares of gypsum (23.71%) and halite (12.71%) are also significant. The Zhilyan salt has a more concentrated potassium content (77.4% of carnallite), contains less halite (8%) and does not contain sulphur and insoluble residue in the form of calcium sulphate. This will allow us to significantly facilitate further raw material processing and obtain a ballast-free mineral fertiliser. Magnesium content is also sufficient in its composition (Table 3).
When processing the carnallite ore, a method of incomplete salt dissolution was chosen to remove sodium chloride as a salt with greater solubility [14]. Based on the analysis of known methods for enriching polyhalite ore, a temperature of 20°C and a time interval of 10 - 40 minutes
Mineral | Carnallite | Gypsum | Halite | Glaserite | Langbeinite | Moisture |
---|---|---|---|---|---|---|
KCl·MgCl2·6H2O | CaSO4·2H2O | NaCl | К2SO4·Na2SO4 | K2SO4∙2MgSO4 | Н2O | |
Chelkar salt | ||||||
Content, mass (%) | 33.5 | 23.71 | 12.71 | 17.7 | 4.03 | 8.35 |
Zhilyan salt | ||||||
Mineral | Carnallite | Gypsum | Halite | Periklas | Mix of Carnallite and Brucite | Moisture |
KCl·MgCl2·6H2O | CaSO4·2H2O | NaCl | MgO | KMgCl2.5 (OH)0.5 | Н2O | |
Content, mass (%) | 77.4 | - | 8.00 | 10.90 | 3.70 | - |
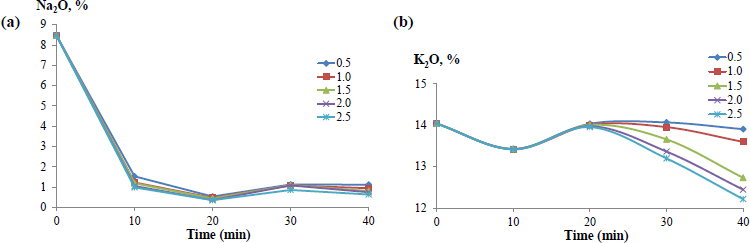
Effect of time on Na2O (a) and K2O (b) content in the solid phase at various water: salt ratios.
for washing the crushed ore from halite were initially selected. The process was studied in a water: salt ratio interval of (0.5 - 2.5): 1 with the simultaneous study of the effect of water consumption on the washing degree. As can be seen in Fig. (4a), Na2O content in the solid phase decreases from ≈ 8.5% to the minimum value of 0.5% by the 20th minute of washing, regardless of the water volume used. At the same time, after 10 minutes, K2O content in the washed ore decreases insignificantly, which is associated with the first dissolution of glaserite, the solubility of which is slightly higher than that of halite (Fig. 4b). Continued ore dissolution for up to 20 minutes leads to K2O content being restored up to its initial value of 14.03%, regardless of the water flow rate supplied for washing. It is caused by the salting out of KCl from the solution upon dissolution of the more water-soluble NaCl salt with the same ion [25].
The results showed that washing for 20 minutes promotes a reduction in sodium salt content in raw materials by more than 15 times with minimal losses of potassium salts. To ensure minimum water input into the potash ore enrichment, it is expedient to carry out the process at a mass ratio of water: salt = 1/2, at which the maximum efficiency of ore washing from sodium chloride is achieved (Fig. 5), and the potassium component is almost completely preserved in the washed ore [25].
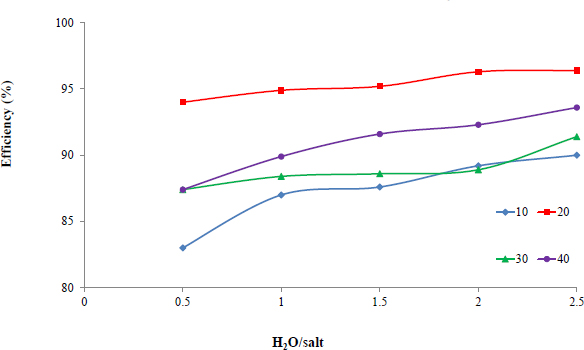
Dependence of washing degree on the water: salt ratio under various process times (min).
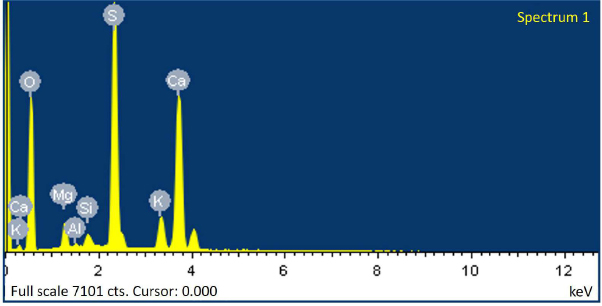
SEM analyses of the ore after double washing.
Element | Ore after Double Washing from Sodium Chloride | |
---|---|---|
Weight Composition (%) | In Terms of Oxides (%) | |
O | 47.39 | - |
Mg | 5.03 | 8.38 |
Al | 0.23 | 0.43 |
Si | 0.62 | 1.32 |
S | 18.52 | 55.56 (SO42-) |
K | 9.79 | 11.80 |
Ca | 18.42 | 25.79 |
In industrial conditions, the production of water-soluble salts of potassium, sodium and magnesium is organised according to a scheme with minimal water input into the process by using circulating mother liquor instead of water to dissolve. Therefore, the efficiency of washing the potassium ore from sodium salts in two- and three-fold washing modes was studied under established optimal conditions for ore enrichment by the potassium component. The results show that when washing the ore with the first filtrate, potassium content in the solid phase increases due to the additional dissolution of sodium salts by a filtrate, which already contains 3.02% K2O and 7.84% Na2O. In this case, potassium and sodium salts are salted out. During washing, sodium chloride is predominantly dissolved, and sodium sulphate is salted out into the solid phase. Carrying out the third washing causes a decrease in potassium content in the sediment and an increase in sodium content, which will reduce the washing efficiency. Therefore, to ensure high efficiency of ore enrichment for potassium, it is expedient to propose washing the ore twice, first with the first filtrate (wash water) and then with water. The efficiency of double washing is confirmed by the results of the SEM study (Table 4); a spectrogram shown in Fig. (6) indicates an absence of sodium chloride in the washed ore.
To separate the insoluble calcium sulphate and to reach complete dissolution of potassium and magnesium sulphates, which are the target components for obtaining the mineral fertiliser, chemical conversion methods are required. The chemical composition of raw materials presented in Table 4 suggests that the main water-soluble components are potassium and magnesium sulphates bound to an insoluble calcium sulphate. To extract them from ore into water-soluble compounds, the process of dissolving the washed potassium ore with the nitric acid solution was studied [26]. The process is described in the main reaction Eqs. (1 and 2):
![]() |
(1) |
![]() |
(2) |
Due to the fact that the interacting compounds are strong electrolytes, these reactions are reversible ion exchange reactions occurring in an aqueous solution. They proceed until an equilibrium is established since, according to the theory of electrolytic dissociation, all reagents and products are in the solution in the form of ions [27]. When strong electrolytes interact in a solution, ionic equilibrium is established instantly. Such reactions are written in ionic form (3) and (4):
![]() |
(3) |
![]() |
(4) |
When a nitric acid solution interacts with an enriched potassium-magnesium salt, the dissolution of potassium and magnesium sulphate occurs due to the ionic strength of the acid. Moreover, since the reactions proceed without the formation of precipitate or gas, then the interaction of reagents is represented by the transfer of potassium, magnesium and sulphate ions into the solution with the formation of a solution of equilibrium composition.
According to scientists [28], “in an irreversible process, no useful work is performed, and, therefore, the Gibbs energy should decrease, i.e., ΔG < 0. Only such a process can proceed spontaneously. In a reversible process, maximum useful work is performed due to the decrease in Gibbs energy: ΔG = −W′max. In the case of a small absolute value of ΔG°, a state of chemical equilibrium is established at comparable concentrations of initial substances and products. With a small positive value of ΔG°, a reaction in the reagents’ mixture (at first, there are no reaction products) still proceeds in the forward direction until a certain small amount of products is formed. If ΔG° is large, then the reaction practically does not proceed from the very beginning. A non-spontaneous reaction can occur without the expenditure of work as a result of a shift in equilibrium according to the Le Chatelier principle” [28].
Thermodynamic probability of the reactions’ occurrence, calculated as Gibbs energy at temperatures of 20, 30, 40 and 50°С confirms the formation of an equilibrium solution since the change in Gibbs energy for reaction (1) is close to zero throughout the entire temperature range, ranging from +1.5 to +3.5 kJ/mole, as shown in Fig. (7) for reaction 1.
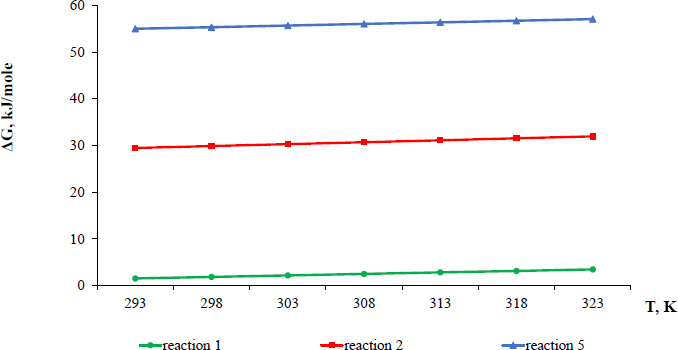
Gibbs energy dependence on temperature.
As the equilibrium condition is ΔG = 0, the ΔG value of reaction (1) corresponds to a system state close to the equilibrium and does not indicate a thermodynamic prohibition of the reaction itself. ΔG values for reaction (2), equal to ≈ +30 kJ/mole, as shown in Fig. (7), indicate a thermodynamic impossibility of an interaction between magnesium sulphate and nitric acid. However, at the same time, low positive values of Gibbs energy characterise, as for reaction (1), a possibility of a reaction (2) with dissolution of a small part of the magnesium salt until an equilibrium is established in the system in regards to magnesium.
The remaining part probably remains in the solid phase. The interaction of insoluble calcium sulphate in ore composition with nitric acid is described by the reaction Eq. (5):
![]() |
(5) |
Gibbs energy for reaction (5) over the entire temperature range takes positive values from +55 to +57 kJ/mole, which confirms that reaction (5) is thermodynamically impossible; therefore all calcium sulphate remains in the solid phase (Fig. 7). Therefore, a chemical method for processing of enriched ore with a nitric acid solution was used to separate the insoluble calcium sulphate.
Kinetics of washed potash ore decomposition with 10% nitric acid was preliminarily studied. As the results show, equilibrium in the system for potassium and magnesium is achieved within 30 minutes [26]. To calculate the kinetic parameters of the decomposition process in the interval of 10-30 minutes, an order of main reactions (1) and (2) and rate constants were determined, taking into account the experimental values of K2O and MgO content. Their contents are given in Table 5.
Temperature (°С) | Component | Concentration | Time (min) | |||
---|---|---|---|---|---|---|
10 | 20 | 30 | 40 | |||
50 | K2O | С, mole/l | 0,13 | 0,314 | 0,44 | 0,45 |
lgC | -2,04 | -1,139 | -0,800 | -0,798 | ||
40 | K2O | С, mole/l | 0,095 | 0,165 | 0,27 | 0,28 |
lgC | -1,02 | -0,782 | -0,57 | -0,55 | ||
50 | MgO | С, mole/l | 0,19 | 0,39 | 0,59 | 0,58 |
lgC | -0,72 | -0,41 | -0,229 | -0,236 |
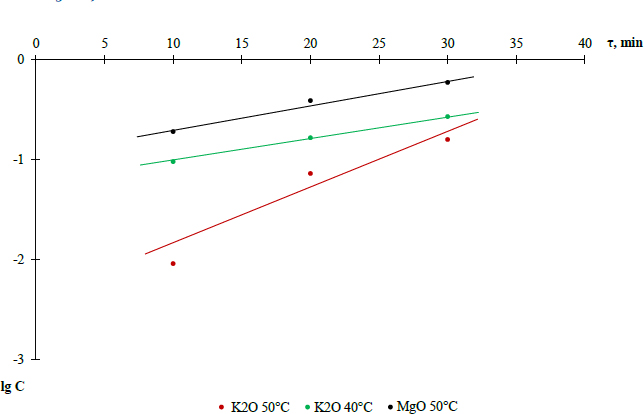
lgC dependence on process time.
Based on the data, the dependence of K2O content in the solution on time was plotted, shown in Fig. (8).
The reaction (1) order (n) was determined by the Van't Hoff method using the logarithm of the ratio of reaction rates and concentrations at two times:
![]() |
(6) |
![]() |
The reaction (2) order was determined similarly:
![]() |
Straight lines of the dependence lgC=f(τ) indicate the 1st order of reactions (1) and (2). Consequently, the rate of these reactions is described by the first-order equation V=k·C, and the rate constant is determined by Eq. (7):
![]() |
(7) |
The reaction rate constants for temperatures of 50 and 40°C are equal, respectively, 0.09 min-1 and 0.055 min-1. Then, to determine the reaction activation energy in the optimal mode, the Arrhenius equation was applied.
![]() |
(8) |
where k = reaction rate constant;
k0 = pre-exponential multiplier (calculates the number of molecule collisions, their special orientation and other factors that do not depend on temperature);
R = universal gas constant;
E = reaction activation energy.
This equation describes the dependence of the reaction rate on temperature. The ratio of rate constants at different temperatures is expressed as:
![]() |
Next, the activation energy of reaction (1) was determined as E= 41.37 kJ/mole, which indicates the internal kinetic region of the process behaviour. In this region, the process rate is determined by the rate of chemical reaction, which increases only with increasing temperature and does not practically depend on the rate of diffusion stages. Therefore, 50°C was chosen as the optimal temperature for nitric acid decomposition of enriched ore, which ensures the maximum process rate [26, 29].
The study of this salt processing in the range of nitric acid concentrations of 10-30% showed that when concentration increases to 20%, 100% extraction of potassium salts into the liquid phase containing 4.5% K2O is achieved. At the same time, MgO content in the solid phase increases and the content of sulphate ions in the liquid phase decreases, which is caused by the salting out of magnesium sulphate from the solution. This is confirmed by the results of the thermodynamic study, according to which a reaction (2) is thermodynamically impossible but has low positive values of Gibbs energy, which is associated with high ionic strength of the nitric acid solution, which partially transfers magnesium salts into the liquid phase.
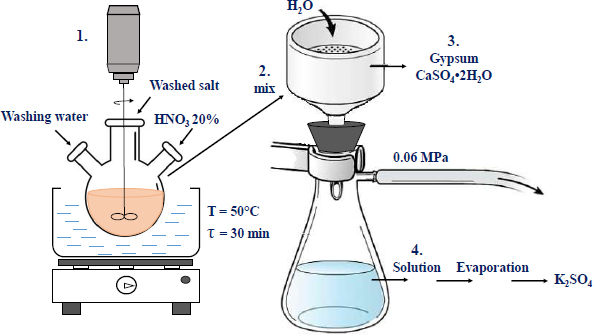
Scheme of nitric acid decomposition of enriched potash salt.
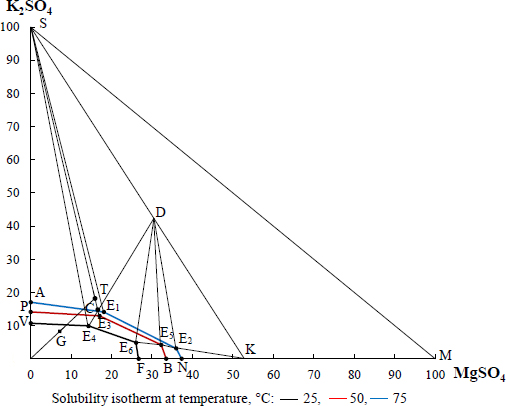
Solubility in K2SO4-MgSO4-H2O system.
In addition, calcium oxide is practically absent in the liquid phase and its content is determined by solubility in nitric-acid extract, therefore, calcium is completely bound in the form of insoluble calcium sulphate. The results of the study concluded that 20% nitric acid should be used to decompose washed ore.
The formed suspension was separated by vacuum-filtration, then the precipitate was washed with hot water and dried, and the nitric acid extract was further processed to obtain the target product. The scheme of this process is given in Fig. (9).
The final solution obtained in optimal decomposition mode contains 8.34% K2SO4, 7.62% MgSO4, and 2.03% N. Then, two-stage crystallization of potassium salts was carried out using an isothermal method, considering the initial solution composition in point G and crystallization fields on the solubility diagram in the K2SO4-MgSO4-H2O system, presented in Fig. (10).
In determining the type and amount of crystallising salt during solution evaporation, the content of nitrate ions was not taken into account. Chemical analysis determined the composition of the solution obtained in optimal decomposition mode, namely: 4,51% K2O, 2,54% MgО, 10,9% SO42- and 2,03% N. The evaporation process is depicted in the diagram as the evaporation beam OT. At a temperature of 75°C, the system is in the field ASE1 of potassium sulphate crystallisation. To crystallise this salt, about 60% of the water should be evaporated from the extract, which is shown by the GT segment. In these conditions, a pure salt of potassium-magnesium sulphate was obtained, since the figurative point of system composition was in the field of joint crystallization of potassium sulphate and a double salt. This salt composition is shown in Table 6. Its content practically corresponds to the crystalline hydrate composition indicated by the XRD analysis in Fig. (11a).
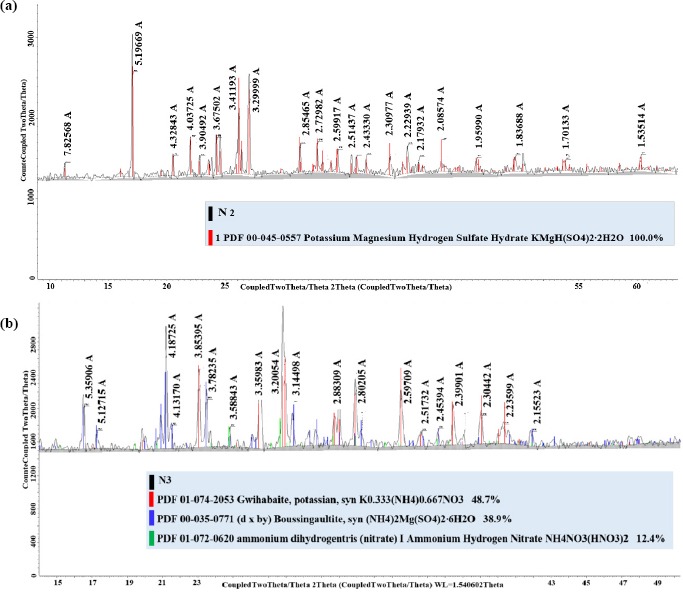
XRD patterns of salts obtained by isothermal crystallization (a) and by ammonization, evaporation and drying of the mother liquor (b).
- | Content in the Product (%) | |||
---|---|---|---|---|
Component | K2О | MgО | N | SО42- |
After partial evaporation | 20.44 | 10.76 | - | 55.71 |
After ammoniation and drying | 13.99 | 5.45 | 15.33 | 28.24 |
The product does not contain nitrate ions, which once again confirms the crystallisation of only potassium and magnesium sulphates from the filtrate. Its composition is shown in Table 6.
The mother liquor was ammoniated to pH = 6 to obtain a neutral product and dry; as a result, the potassium-nitrogen-magnesium salt crystallises, and double salts are identified by the XRD analysis shown in Fig. (11b). The obtained salt does not contain insoluble impurities and chlorine and consists of potassium ammonium nitrate and magnesium ammonium sulphate. Its chemical composition is shown in Table 6.
The new products are non-hygroscopic,completely water-soluble fertilisers that are easily digestible and necessary for feeding many vegetable and fruits.
As a result of nitric acid decomposition of potash ore, an insoluble precipitate of calcium sulphate is formed in the form of gypsum, which is a production waste. After separating the insoluble residue in a vacuum filter and washing twice, this by-product successfully passed tests for compliance with its normally hardening gypsum binder, which can be used as a binder in the construction industry.
CONCLUSION
Chemical and mineralogical compositions of potassium rocks from two earlier unexplored deposits were determined as a result of the research. Both of these salts are of carnallite nature. The reserves amount to more than 2 billion tonnes. The Chelkar ore contains, in addition to carnallite, many impuritie represented by sodium and calcium compounds. However, the Zhilyan salt differs in its higher potassium content and an absence of calcium and sulphur in its composition. According to this analysis, the effective processing method of the natural salts was studied and developed to obtain ballast-free potash fertilisers. It includes the removal of sodium chloride from the natural system by incomplete dissolution, nitric acid decomposition of the enriched salt and target salts crystallization from the extract. Thermodynamic analysis was performed in detail and the kinetics of decomposition of washed salt was studied. This made it possible to establish the internal kinetic region of behaviour, optimal temperature of the process and probability of partial transition of the magnesium salt into a solution.
Based on research results, new effective methods for producing chlorine-free water-soluble potassium and potassium-nitrogen fertilisers from the Chelkar deposit ore have been proposed. These methods are characterisedby minimal water input, absence of production waste and a possibility for integrated use of all components of this natural salt. The proposed innovative method for carnallite ore processing provides for obtaining more efficient water-soluble and environmentally friendly potash fertilisers without industrial waste. The insoluble residue of gypsum is environmentally friendly due to an absence of impurities and it can be used as a gypsum binder in the construction industry. This research is critical because it not only identifies new sources of potash raw materials but also introduces an innovative processing method not previously used, which could significantly impact the global agricultural sector.
AUTHOR’S CONTRIBUTION
The authors confirm their contribution to the paper as follows: AA contributed to the writing – original draft, methodology, formal analysis, funding acquisition and investigation of the study and GS was involved in the writing, review and editing, methodology, formal analysis, visualization and validation. All authors have read and agreed to the published version of the manuscript.
LIST OF ABBREVIATIONS
PFA | = Flame photometric analyser |
XRD | = X-ray diffraction |
SEM | = Scanning electron microscopy |
AVAILABILITY OF DATA AND MATERIAL
All data generated or analysed during this study are included in this published article.
FUNDING
This research is funded by the Committee of Science of the Ministry of Science and Higher Education of the Republic of Kazakhstan (Grant No. AP19175404).
ACKNOWLEDGEMENTS
Declared none.