All published articles of this journal are available on ScienceDirect.
Mining Waste in the Southern Urals as a Source of Minerals
Abstract
Background
In the context of the depletion of natural resources, the issues of using man-made waste as a source of minerals are becoming especially relevant. The mining and processing industry is one of the leaders in the production of man-made waste.
Objective
The purpose of this study is to demonstrate the enrichment of waste from mining and processing plants and tailings dumps of gold ore deposits in the Southern Urals with Au, Cu and Zn, which can be used for their re-extraction, and also to understand the need for the environmental and economic feasibility of their processing.
Methods
Analytical studies were carried out using X-ray fluorescence, atomic absorption and energy dispersive methods.
Results
The dumps and tailings of pyrite mining and processing plants and slags of copper smelters of the Southern Urals contain increased concentrations of Au, Cu and Zn. The Zn content is comparable to its percentage content in currently mined ores. It was established that the tailings of the Ulyuk-Bar gold deposit contain increased contents of Au and Ag, which leads to their annual losses reaching 150 and 55 kg, respectively.
Conclusion
Our research confirms the urgency and significance of the problem of development and comprehensive use of the resource potential of man-made deposits, which requires further study and development of effective technologies.
1. INTRODUCTION
Population growth contributes to an increase in the consumption of minerals, which leads to an intensification of the extraction of mineral resources. This trend leads to an increase in the amount of man-made waste generated and, as a consequence, a negative impact on the environment [ 1 ]. Issues of ecology, resource conservation and energy conservation are currently coming to the forefront. The ideology of unlimited technical progress is giving way to the concept of sustainable development, taking into account the interests of not only the present but also future generations [2-4]. One of the areas of implementation of this concept is the use (recycling) of production and consumption waste that accumulates in dumps and landfills and represents man-made raw materials [5-7].
The largest amount of industrial waste is produced by the extractive industries. Of the huge amount of mineral raw materials extracted from the natural environment for production purposes, only 1.5-2.0% is converted into the final product [8], and the bulk of it (over 90%) is converted into industrial waste, which includes high concentrations of heavy metals (Cu, Cd, Fe, Mn, Pb, Zn), metalloids (As, Se), and precious metals (Au, Ag) [3-7].
The use of mining waste is a major environmental issue worldwide [ 9 ]. Mineral reserves are limited and are gradually being depleted. The use of secondary resources reduces the extraction of minerals from primary sources, minimizes the destruction of the ecosystem, and facilitates the transition to a closed-loop economy. In addition, the processing of industrial waste is cheaper than the development of new deposits, which may be located in hard-to-reach areas. This reduces the cost of extraction and increases the profitability of enterprises [ 1 ].
The problem of mineral waste is relevant for this industry throughout the world. The mining industry has traditionally been a source of generation and accumulation of large quantities of waste. Thus, according to European statistics, in 2022, mining and quarrying occupied second place – 22.7% of the total waste generated (construction occupied first place – 38.4%). Of the total waste generated in the EU in 2022, 64% (3.2 tonnes) per inhabitant was major mineral waste [10]. The data from the U.S. Environmental Protection Agency (EPA) shows that in 2022, 2.59 million tons of mining production resulted in the generation of 0.67 million tons of waste, 96.6% of which were disposed of or otherwise released into the environment [11].
The total value of metals in waste is estimated to be comparable to the value of potential mineral resources and several times exceeds the value of explored reserves in the subsoil that are not yet used. In most cases, mineral waste is used for the construction industry (no more than 10%). In technologically advanced countries, more than 40% of copper, 35% of gold and a significant amount of other metals are obtained from waste using new technologies, such as leaching [ 12 ]. Numerous studies confirm both the environmental and economic benefits of recycling mining waste [ 13-15].
The problem of waste generation, accumulation, storage, and disposal is extremely acute for Russia and affects almost all its regions. There is a steady increase in waste generation in the Russian Federation. Thus, according to data from 2014 to 2023, the increase in industrial waste production amounted to 55.7% (from 5168.3 to 9278.8 million tons) [16]. Despite the fact that the share of recycled waste increased by 60% during the period under review, and in 2023 it amounted to only 42.6%. At the same time, if in Europe more than 50% of waste is recycled, then in Russia the average level of industrial waste recycling is 35%. The rate of waste generation growth increases annually and, over the past few years, has amounted to 15-16%. The main sources of waste are still enterprises of the fuel and energy complex, mining, forestry and woodworking industries. Thus, in many regions of the country, huge reserves of mine rocks, ash and slag mixtures, and other waste from the mining, coal mining, and metallurgical industries have accumulated [8, 17, 18].
Many waste dumps, in terms of the volume of stored rocks, their composition, properties and suitability for obtaining useful products, represent man-made deposits of minerals [19-21]. Despite the significant volumes of man-made accumulations, the level of their utilization remains low [22-28]. Thus, Russian mining enterprises annually store about 5 billion tons of overburden and waste rock on the surface, and about 700 million tons are delivered to waste heaps by enrichment plants [23]. Tailings of mining and processing plants store up to hundreds and tens of thousands of tons of those ores, the percentage content of extracted elements which is lower than the industrial one [29, 30].
In the Ural region, man-made deposits are widespread, representing waste from mining, processing, metallurgy and other industries and suitable in quantity and quality for industrial use [31, 32]. The concentration of ore and impurity elements often exceeds their content in natural deposits.
Significant copper reserves (almost 20 million tons) are contained in numerous deposits in the Southern and Middle Urals, most of which are of the copper-pyrite type. At the same time, over the past 50 years, the content of the main valuable components in the mined ore at the copper-pyrite deposits of the Southern Urals has significantly decreased [33, 34]. The copper content has decreased by 2.6 times and zinc by 3.1 times. Currently, the copper content in mined ores fluctuates at the level of 1.5-1.8 wt. %, zinc – 0.5-0.7 wt. % [35]. At the same time, the share of refractory ores has increased from 15 to 40% of the total mass of processed raw materials, and this is typical for mining enterprises developing deposits of multicomponent ores.
Pyrite concentrates and cinders are valuable types of man-made mineral and chemical resources stored by mining and processing plants during the enrichment of sulfide copper and lead-zinc raw materials. Both types of resources are enriched in iron and sulfur, non-ferrous (Cu, Zn, Pb, Co, Sb, etc.), noble (Au, Ag), and dispersed rare metals (Se, Te, Bi, Cd, Tl, etc.). Copper ore mining and processing plants in the Urals have already accumulated 50 million tons of pyrite in enrichment tailings [36, 37]. The pyrite content in ores is 60-80%, and in tailings – 90-95%. Pyrite cinders as waste from former sulfuric acid production are currently concentrated in 4 largest storage facilities with a capacity of over 1 million tons each: Ammofos OJSC (Cherepovets) – 12 million tons, Meleuz Mineral Fertilizer Plant – 2.5 million tons, explored Kirovograd deposit – 7 million tons, PMCPA PJSC (Krasnokamensk) – 4.5 million tons, that is, in total – 26 million tons. The only consumer of pyrite cinders at present is the cement industry, where pyrite iron is used to form calcium aluminoferrite binder. The task of using pyrite raw materials as a complex source of metal products was set in the late 30s of the last century. According to studies [36, 38], pyrite cinders contain 1.1-2.1 ppm Au, 20-30 ppm Ag, 0.3-0.4% Cu, and 0.7-1.0 wt. % Zn and 40-50 wt. % Fe, and 0.5 tons of gold are lost annually with their deliveries to cement plants. In particular, up to 10 tons of Au have been shipped to Novorossiysk cement plants in pyrite cinders over 50 years [38]. In general, according to data [39], Au losses during enrichment of pyrite ores in Russia amount to 50-60%, with a significant portion of the losses coming from pyrite containing Au.
According to previous studies by the authors [40, 41], the waste of copper-zinc ores from mining and processing plants in the Southern Urals contains elevated Au contents of up to 1 ppm, as well as Zn, which reach industrial levels.
This article presents an analysis of the chemical composition and content of useful components in ash and slag mixtures of the Sibay copper smelting plant, dumps and tailings of the Gay, Buribay, Sibay, Uchaly mining and processing plants of pyrite ores in the Southern Urals, as well as tailings of the Ulyuk-Bar gold deposit. The purpose of this study is to determine the presence of possible useful components in them, including Au, Ag, and non-ferrous metals, based on determining the chemical composition of waste from mining and processing plants and tailings, which can be used for their repeated extraction and waste processing.
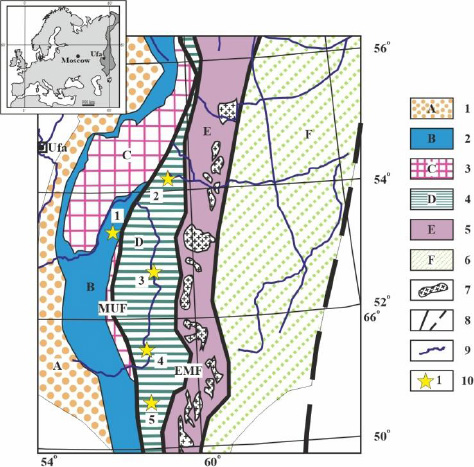
Structural zones of the Southern Urals and the location of the Ulyuk-Bar gold deposit and mining and processing plants of pyrite-polymetallic ores [43]. Note: 1 – Preuralian foredeep, filled with Permian molasse; 2 – West Uralian zone, with a predominant development of in-tensely folded and westward-thrust Paleozoic shelf and bathyal (passive margin) sedimentary sequences; 3 – Central Uralian zone, with exhumed Precambrian complexes; 4 – Tagil-Magnitogorsk zone with the mostly Paleozoic ocean floor and island arc formations; 5 – East Uralian zone, containing a combination of Precambrian and Paleozoic oceanic and island arc complexes; 6 – Transuralian zone, composed of pre-Carboniferous complexes; 7 – Main Granite Axis; 8 – Мulti-scale tectonic faults: MUF − Маin Uralian Fault, EMF – East Magnitogorsk Fault; 9 – Rivers; 10 – Research objects: 1 – low-sulfide gold-quartz deposit Ulyuk-Bar; 2-5 – mining and processing plants of pyrite-polymetallic ores: 2 – Uchaly, 3 – Sibay; 4 – Buribay; 5 – Gay.
2. MATERIALS AND METHODS
A total of 29 samples were selected from the Ulyuk-Bar dumps and tailings of gold ore deposits (n = 15) (Fig. 1, number 1), mining and processing plants (Gai (n = 2), Buribay (n = 2), Uchaly (n = 2), Sibay (n = 4)) (Fig. 1, numbers 2–5), as well as slag from the Sibay copper smelting plant (n = 4). Samples weighing 0.5 kg were crushed to a fraction of <1 cm, then averaged to weigh ~150 g, which were completely ground to a fraction of ~0.074 mm and analyzed using various methods. The concentrations of petrogenic oxides and rare elements in rocks and veins (SiO2, TiO2, Al2O3, Fetotal or Fe2O3total, MnO, CaO, MgO, Na2O, K2O, Stotal, P2O5, V, Cr, Co, Ni, Cu, Zn, As, Ba, Pb) were determined by X-ray fluorescence analysis using a spectrometer XRF (X-Calibur, Xenemetrix LTD., Migdal HaEmek, Israel) (Ag-anode, 15-50 kV, 60-1000 mA) [42]. Samples (5 g) for analysis were ground together with 5 drops of polyvinyl alcohol, dried at room temperature, and pressed at a pressure of 25 t/cm2. Calibration curves were constructed using state reference materials of iron and polymetallic ores (182-89, 183-89, 184-89, 508-11, 509-11, 2884-84, 3031-84, ОР-1, ОР-2, ОР-3, ОР-4). For Au analysis, 5–10 g powdered (~0.074 mm) samples were calcined together with ammonium nitrate at 450–650°C for 4.5–6 h, followed by acid digestion with hydrochloric acid, a mixture of nitric and hydrofluoric acids, and aqua regia. In order to concentrate and isolate gold from interfering elements, it was extracted with butyl acetate from a hydrochloric acid solution (1/7) at an aqueous-to-organic phase ratio of 10:1. The detection limit while measuring petrogenic oxides and rare elements was 0.01-0.2 wt % and 3-10 ppm, respectively.
The concentrations of Au and Ag were determined by atomic absorption analysis using a Persee A3 spectrometer (PG General Instrument Co., Beijing, China) [42]. In order to concentrate and isolate gold from interfering elements, it was extracted with butyl acetate or isoamyl alcohol from a hydrochloric acid solution (1/8) at an aqueous-to-organic phase ratio of 10:1. The detection limit in the measurement of Au and Ag comprised 0.1 ppm.
The composition study of minerals of Ulyuk-Bar gold deposit tailings dumps (n = 4) of the ore occurrence was carried out in polished thin sections by analyst S.S. Kovalev using a Tescan electron microscope (Vega 4 Compact, Tescan Brno s.r.o., Brno, Czech Republic) equipped with an Explorer 15 energy dispersion analyzer (Oxford Instruments, Oxford, UK) [42]. Spectra were processed automatically in the AzTec One software package using the TrueQ procedure (version 5.1, Oxford Instruments, Oxford, UK). During the analysis, the following parameters were used: an acceleration voltage of 20 kV, a probe current of 4 nA, 60 s spectrum point accumulation time in the Point&ID mode, and a beam diameter of ~3 µm.
3. RESULTS AND DISCUSSION
In the analyzed samples of dumps and tailings storage facilities of the Gay, Buribay, Uchaly, and Sibay Mining and Processing Plants, the Cu content was found to be at the level of 0.05-0.17 wt. %, Zn – 0.05-0.37 wt. % (Table 1). The calculated pyrite content in them based on Stotal is 4-40%. It should be noted that the obtained data contain a significant dispersion in the contents of the main rock-forming elements, which reflects the mineralogical heterogeneity of the composition of the dumps and tailings storage facilities, noted earlier [35]. In the Sibay dumps, judging by the ratio of Fe, Stotal and LOI contents (see Table 1, column 9), hydrous sulfates are present to a significant extent, probably formed during the hypergene alteration of the original rocks. Noteworthy is the slight increase in the Cu and Zn contents, the extraction of which requires different schemes compared to those for primary, slightly altered waste dumps.
Component | 1 | 2 | 3 | 4 | 5 | 6 | 7 | 8 | 9 | 10 |
---|---|---|---|---|---|---|---|---|---|---|
SiO2 | 63.04 | 53.28 | 43.33 | 33.28 | 31.58 | 28.29 | 48.22 | 47.87 | 27.83 | 25.40 |
TiO2 | 0.25 | 0.20 | 0.57 | 0.42 | 0.23 | 0.23 | 0.82 | 0.96 | 0.19 | 0.20 |
Al2O3 | 9.34 | 8.51 | 15.31 | 11.81 | 8.40 | 5.46 | 16.26 | 16.10 | 5.10 | 4.60 |
Fetotal | 12.50 | 15.56 | 10.07 | 8.05 | 23.86 | 25.15 | 12.75 | 22.78 | 15.27 | 50.09 |
MnO | 0.04 | 0.03 | 0.25 | 0.13 | 0.08 | 0.05 | 0.04 | 0.05 | 0.06 | 0.07 |
MgO | <0.1 | <0.1 | 3.84 | 4.93 | 6.36 | 6.39 | 1.40 | 1.30 | 1.75 | 1.50 |
CaO | 1.72 | 1.85 | 0.25 | 0.27 | 3.42 | 2.76 | 1.23 | 1.38 | 2.62 | 2.29 |
Na2O | <0.5 | <0.5 | 1.92 | 1.84 | – | – | 0.20 | 0.20 | 0.19 | 0.20 |
K2O | 0.64 | 0.49 | 1.65 | 0.94 | 0.61 | 0.49 | 0.63 | 0.66 | 0.39 | 0.37 |
P2O5 | 0.06 | 0.05 | 0.05 | 0.05 | 0.14 | 0.11 | 0.15 | 0.18 | 0.15 | 0.28 |
Stotal | 13.36 | 20.70 | 1.79 | 6.33 | 18.08 | 18.87 | 11.59 | 5.61 | 27.51 | 9.02 |
LOI | – | – | 15.10 | 27.45 | – | – | 7.04 | 2.78 | 19.17 | 5.14 |
Sc | 11 | 13 | 25 | 17 | 13 | <10 | 11 | 17 | 17 | 12 |
V | 74 | 74 | 282 | 172 | 81 | 64 | 118 | 136 | 46 | 59 |
Cr | 23 | 31 | – | – | 15 | <10 | 190 | 234 | 44 | 34 |
Co | 44 | 58 | 42 | 47 | 30 | 27 | 43 | 85 | 70 | 164 |
Ni | 18 | <10 | 34 | 39 | 105 | 104 | 79 | 74 | 21 | 27 |
Cu | 1563 | 1664 | 515 | 689 | 1551 | 930 | 1062 | 1195 | 1319 | 1508 |
Zn | 978 | 2163 | 325 | 471 | 3664 | 3020 | 992 | 1105 | 1236 | 1489 |
As | – | – | – | – | – | – | 1469 | 1555 | 1732 | 486 |
Ba | 1589 | 1382 | 174 | 101 | 236 | 279 | 980 | 1783 | 1848 | 3843 |
Pb | 52 | 35 | <10 | 13 | – | – | 139 | 273 | 34 | 66 |
Component | 1 | 2 | 3 | 4 |
---|---|---|---|---|
SiO2 | 28.54 | 27.78 | 25.93 | 26.61 |
TiO2 | 0.10 | 0.09 | 0.09 | 0.09 |
Al2O3 | 2.08 | 1.93 | 1.71 | 1.76 |
Fe2О3total | 44.49 | 44.06 | 44.38 | 43.92 |
MnO | 0.05 | 0.05 | 0.03 | 0.05 |
MgO | 0.49 | 0.21 | 0.51 | 0.88 |
СаО | 5.62 | 5.61 | 5.54 | 5.54 |
K2O | 0.35 | 0.31 | 0.29 | 0.30 |
P2O5 | 0.07 | 0.07 | 0.09 | 0.07 |
Stotal | 3.00 | 2.97 | 2.94 | 2.83 |
Sc | 15 | 12 | 15 | 16 |
Ni | 13 | 15 | 22 | 20 |
Cu | 1780 | 1600 | 1420 | 1620 |
Zn | 20062 | 10932 | 20257 | 20120 |
Рb | 50 | 39 | 23 | 11 |
The highest zinc contents (0.30-0.37 wt. %) established by us in the dumps and tailings of the Uchaly Mining and Processing Plant are comparable to those in the mined ores. For example, as noted above, today the zinc content in them is 0.5-0.7 wt. % [35]. In addition, it should be noted that in the pyrite concentrate isolated from the samples of the dumps and tailings of the Gai Mining and Processing Plant, we also established gold contents at the level of 0.8-1.2 ppm (atomic absorption analysis) [40]. This is in good agreement with previously conducted studies. As established in the works [44], the ore of the Gai deposit contains various generations of pyrite, differing in habitus and different gold content from <0.5 to more than 9 ppm, and other impurities.
The results we obtained are consistent with the literature data, according to which the tailings of the Ural enrichment plants contain (in wt. %) 0.3-0.4 Zn, 0.2-0.3 Cu, 20-35 S, and more than 35 Fe [34]. The amount of tailings generated as a result of enrichment production annually amounts to 5-7 million tons. The total value of metals accumulated in the mining waste of Russia and extracted technologically, according to experts, is 4 times higher than the value of their known reserves in the subsoil, which is not yet used. In terms of total reserves, the tailings storage facilities of the Ural enterprises significantly exceed many deposits [34]. In addition, the use (on an industrial scale) of waste from the extraction and processing of minerals will ensure the environmental rehabilitation of territories exposed to the negative impact of economic activities [45-47].
Technogenic raw materials are competitive, promising mineral resources, the use of which provides not only a significant technical and economic effect but also an environmental effect achieved as a natural consequence of the new level of requirements of modern production [31, 34, 35]. It should be noted that at present, in the field of processing waste from mining and processing enterprises, research is being conducted to create new technologies for extracting valuable components from ore processing waste, combining physicochemical enrichment methods (flotation, electrochemistry, etc.) with chemical and metallurgical methods (pyro- and hydrometallurgy, autoclave leaching, biological oxidation) [35, 39, 44, 48-50].
The following types of industrial and household waste can be considered as technogenic raw materials from which useful products can be obtained on an industrial scale: coal mining and combustion waste – mine dumps and ash and slag waste; mining and processing plant waste; metallurgical slag; oil-containing waste and drilling mud; associated petroleum gas; washing and wastewater from enterprises; solid household waste from cities and agglomerations [51-58]. Thus, in the composition of metallurgical slags of the old Sibay copper smelting plant, we have established increased concentrations of Cu at a level of 0.14-0.18 wt. % and very high “ore” contents of Zn, amounting to 1.9-2.3 wt. % (Table 2).
The low-sulfide gold-quartz deposit Ulyuk-Bar is located in the Riphean sediments of the western slope of the Southern Urals. We analyzed samples from its current tailings after the start of development in 2019-2020 by StroyTechInvest LLC (Fig. 2a-c). The deposit's ores are represented mainly by sandstones, to a lesser extent siltstones, and shales, containing gold of 1.7 ppm on average, according to the study of several process samples in 1980 (materials of A.S. Timoshenko and R.G. Safonova). Development is carried out at a gold recovery plant located next to the deposit (Fig. 2b, number 1). The wet gravity concentration method is used based on a mobile concentration complex and a TsK-1700 centrifugal concentrator with a capacity of 50-100 tons of ore per day. The beneficiation tailings are sent to the tailings storage facility located at a distance of 100-200 m from the plant (Fig. 2b, numbers 3-4). According to our data, the Au content in the tailings, with fluctuations from 0.1 to 0.6 ppm, averages 0.3 ppm, Ag − 0.1 ppm (Table 3). Gold of the composition Au0.87Ag0.13 is found in rocks mainly in native form and as inclusions in gold-bearing sulfides (pyrite and arsenopyrite) from quartz veins, as well as in goethite, which was formed in hypergenes during oxidation of sulfides (Fig. 3).
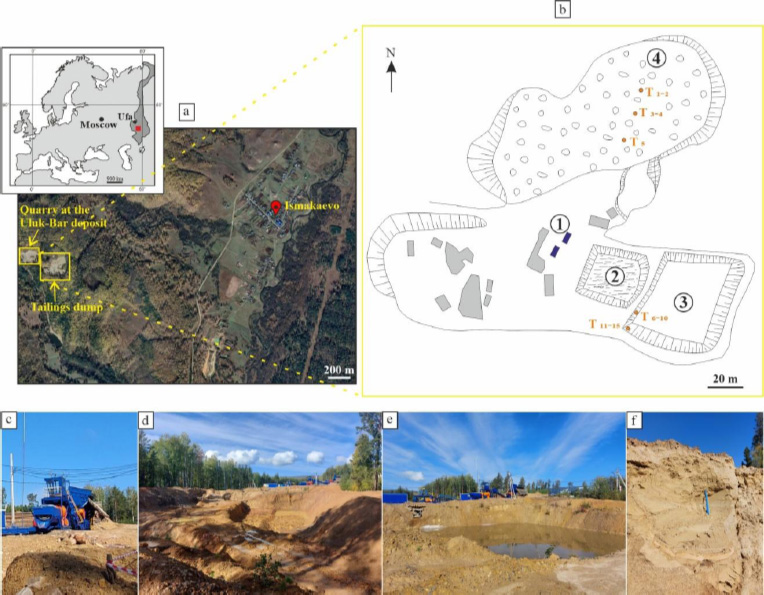
a – location of the Uluk-Bar gold deposit; b – The scheme of the tailings dump and tails-sampling site locations: 1 – gold processing plant, 2 − technological water, 3 – storehouse of fine fraction of tailings (less than 2 mm); 4 − storehouse of overburden and large fraction tailings (over 2 cm); c – installations for wet gravity concentration of gold-bearing ores; d – photo of a storehouse for small fraction tailings; e − photo of technological water; f – tails after concentration of gold.
Component | T1 | T2 | T6 | T7 | T8 | T9 | T10 | T11 | T12 | T15 |
---|---|---|---|---|---|---|---|---|---|---|
SiO2 | 62.79 | 62.74 | 63.74 | 63.91 | 63.70 | 68.64 | 68.85 | 68.89 | 68.76 | 65.61 |
TiO2 | 0.44 | 0.44 | 0.40 | 0.36 | 0.34 | 0.40 | 0.37 | 0.36 | 0.41 | 0.61 |
Al2O3 | 7.40 | 7.31 | 6.66 | 6.44 | 6.19 | 7.67 | 7.65 | 6.90 | 8.06 | 11.84 |
Fe2O3total | 3.38 | 3.21 | 3.07 | 2.75 | 3.15 | 2.92 | 3.02 | 2.70 | 2.92 | 2.94 |
MnO | 0.04 | 0.06 | 0.04 | 0.03 | 0.04 | 0.02 | 0.03 | 0.03 | 0.03 | 0.01 |
MgO | 0.54 | 0.57 | 0.51 | 0.51 | 0.51 | 0.73 | 0.76 | 0.68 | 0.79 | 0.94 |
CaO | 0.07 | 0.05 | 0.08 | 0.04 | 0.05 | 0.20 | 0.15 | 0.13 | 0.11 | 0.13 |
Na2O | 0.15 | 0.20 | 0.13 | 0.40 | 0.14 | 0.30 | 0.23 | 0.12 | 0.18 | 0.17 |
K2O | 0.74 | 0.87 | 0.64 | 0.54 | 0.50 | 0.66 | 0.66 | 0.46 | 0.73 | 1.41 |
Stotal | bdl | bdl | bdl | bdl | 0.03 | bdl | 0.03 | bdl | 0.07 | 0.05 |
Cr | 111 | 90 | 108 | 102 | 115 | 114 | 108 | 110 | 114 | 78 |
Ni | 41 | 41 | 42 | 31 | 39 | 35 | 35 | 41 | 31 | 46 |
Cu | 15 | 17 | 16 | 23 | 11 | 17 | 17 | 10 | 18 | 26 |
Zn | 38 | 36 | 30 | 36 | 36 | 35 | 35 | 34 | 34 | 37 |
Ba | 127 | 220 | 114 | 73 | 128 | 55 | 86 | 104 | 137 | 207 |
Pb | 19 | 20 | 23 | 10 | 20 | 26 | 23 | 20 | 33 | 41 |
As | 194 | 210 | 216 | 214 | 237 | 196 | 214 | 164 | 232 | 280 |
Au | - | 0.3 | 0.2 | - | 0.6 | - | 0.3 | - | 0.1 | 0.2 |
Ag | - | 0.1 | bdl | - | bdl | - | 0.1 | - | bdl | 0.2 |
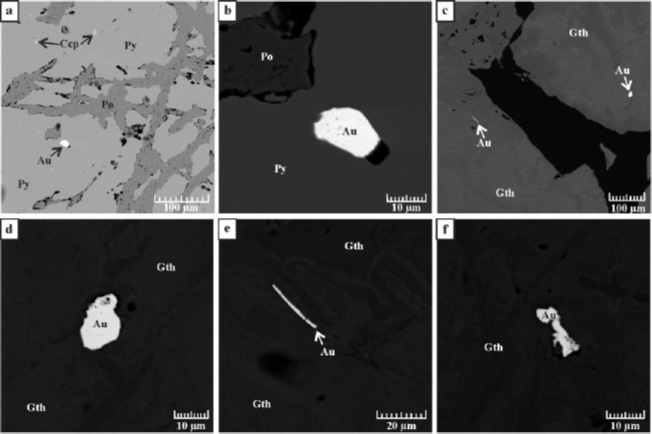
BSE images of heavy fraction minerals in the tailings of the Ulyuk-Bar deposit. a – large oval gold grain in pyrite, which is intergrown with pyrrhotite and has chalcopyrite inclusions; b – enlarged fragment of photo a, gold in pyrite at the boundary with pyrrhotite; c – large oval and elongated rod-shaped grains of native gold in goethite; d, e – enlarged fragments of photo c, gold in goethite; f – xenomorphic gold grain in goethite.
Consequently, the currently used technology allows extracting only about 85% of gold, while 15% is stored in tailings. With this method of extraction, the losses of gold and silver per year will be about 100-150 and 35-55 kg, respectively. To avoid them, secondary processing of tailings is necessary. They are represented by a fine fraction of sandstones and shales (Fig. 2f), less than 1-2 mm, which is very convenient for secondary processing if they contain useful components. Interfering components in the extraction of gold from the tailings of the Ulyuk-Bar deposit may be increased concentrations of Cr (78-147 ppm) and As (136-280 ppm) (Table 3). However, today, there are environmentally friendly complex technologies for gold extraction [59-61]. For example, bio-oxidation of gold and associated metals [62-64], thiosulfate leaching taking into account mass exchange processes [65], leaching of gold concentrated in arsenopyrite with the conversion of arsenic into arsenic glass [66], and other methods that can be successfully used for recycling [67, 68].
Today, there are many methods and technologies for processing mining waste, which at the same time reduce the negative impact on the environment [69-78]. The most effective of them are presented in reference books of the best available technologies. BAT available technologies are a special list of technologies for the production of goods, which establishes standards for the performance of work and the provision of services that correspond to the latest achievements of science and comply with environmental protection criteria. Such technologies help to ensure high productivity of production and prevent negative impact on the environment, taking into account the characteristics of each industry [79-82].
CONCLUSION
Thus, the conducted study shows that the dumps and tailings of copper ore mining and processing plants, slags of old copper smelting plants in the Southern Urals, as well as tailings of a gold ore deposit contain increased concentrations of Au, Cu and Zn. The content of the latter metal is comparable to its percentage content in currently mined ores. Given that deep-seated Cu and Zn deposits are currently being exploited with a high level of economic costs, the processing of old waste from mining and processing plants can be a solution to this problem. Their use is becoming increasingly important due to the obvious need to reduce production costs due to the occurrence of ores at depths of up to 1-1.5 km. In this case, the leading role of not only Au in the extractable value of pyrite as a mineral and chemical raw material, but also the most valuable dispersed rare metals contained in it should be taken into account.
Our research shows that further study should be aimed at finding or improving technologies that allow the processing of multi-component waste in a single cycle. The issues of economic evaluation of such technological cycles that extract several valuable components from mining waste at the same time are becoming relevant.
AUTHORS’ CONTRIBUTIONS
It is hereby acknowledged that all authors have accepted responsibility for the manuscript's content and consented to its submission. They have meticulously reviewed all results and unanimously approved the final version of the manuscript.
LIST OF ABBREVIATIONS
EU | = European Union |
U.S. | = United States |
OJSC | = Open Joint Stock Company |
PJSC | = Public Joint Stock Company |
PMCPA | = Priargun Mining and Chemical Production Association |
LLC | = Limited Liability Company |
BSE | = Backscatter Electron |
BAT | = Best Available Technology |
AVAILABILITY OF DATA AND MATERIALS
The data and supportive information are available within the article.
FUNDING
This study was carried out as part of the IG UFRC RAS State assignment (state registration No. FMRS-2025-0017), Russia.
ACKNOWLEDGEMENTS
Declared none.