All published articles of this journal are available on ScienceDirect.
Thermodynamic Analysis of Isosynthesis Reaction
Abstract
Background
Isobutene is important in the industry as it is used as an intermediate product or direct raw material to produce many chemicals. The primary production method for light olefins is steam cracking of petroleum-based (insufficient resource) naphtha. The steam cracking method consumes a lot of energy, causes serious harmful emissions, and poses a fire and explosion hazard if adequate safety precautions are not taken. Obtaining isobutene from synthesis gas, an alternative source, is important in eliminating the mentioned energy, environmental, and safety problems.
Objective
In this study, thermodynamic analysis of the reaction of obtaining isobutene from synthesis gas, which has strategic importance, was aimed by using the traditional stoichiometric method.
Methods
MATLAB program was used in the solution of the equation sets. The effects of temperature(400-1000K), pressure (1-50atm) and feed composition (Case 1: 50%CO+ 50%H2 Case 2: 60%CO+ 40%H2, Case 3: 70%CO+ 30% H2) on CO conversion and isobutene yield values were investigated.
Results
As expected for the relevant reaction, it was observed that the equilibrium conversions decreased with temperature due to the exothermic nature of the reaction. It was shown that isobutene yields exhibited a similar behavior. It was also shown that pressure change had as serious an effect on conversion and yield values as temperature. H2-rich feed composition positively affected CO conversion and isobutene yields. Again, in a H2- rich feed composition, higher conversions (>90%) and yields (⁓25%) were detected at relatively low-pressure operations (5atm).
Conclusion
It is anticipated that the study will contribute to the development of catalysts and chemical reactor designs for isosynthesis reactions.
1. INTRODUCTION
With the developing technology, isobutene has great importance in the industry as it is used directly as a raw material or intermediate product in the production of chemicals such as polyisobutylene and methyl tert-butyl ether, plastics, and even aircraft and automotive fuel [1-3]. Currently, there are main commercial methods for synthesizing olefins from petrochemicals. These include steam cracking of hydrocarbons (such as naphtha, crude oil, gas oil, and LPG), fluid catalytic cracking (FCC), paraffin dehydrogenation, Fischer-Tropsch synthesis, and methanol-to-olefins (MTO). Catalytic cracking is a chemical conversion process that can be employed for a variety of feedstocks. This process occurs by catalytically converting long-chain hydrocarbons and compounds, such as heavy oils and residues, into olefins and fuels. The catalytic cracking process is carried out on a solid catalyst to moderate the cracking conditions, increase the desired products, and improve their selectivity [4]. However, this process was abandoned because it was not economical and also because of the increasing popularity of the steam cracking units at that time. It was stated that methanol has multiple production routes that can be derived from different processes such as fossil fuels, biomass, pyrolysis and waste. It was emphasized that the MTO process requires zeolite-based catalysts, which can be synthesized in laboratories or by modifying naturally occurring zeolites. However, the physico-chemical properties of zeolites and metal-based zeolites can be modified according to the targeted reaction conditions, reactor type and required product distribution [5, 6]. In the review conducted by Almuqati et al. (2024), the technologies used to produce light olefins, as well as the types of feedstocks, the most used catalysts and catalytic reaction mechanisms, were analyzed. It was stated that microwave energy is a promising technology to promote the production of light olefins by catalytic cracking of different feedstocks [7]. Fischer-Tropsch synthesis is the reaction of CO and H2 in the presence of an active catalyst to produce hydrocarbons and alcohols. Despite the long history of the Fischer-Tropsch process, some fundamental issues remain unclear. One of the most important yet difficult tasks in the production of liquid hydrocarbons is the control of selectivity [8]. Catalysts play one of the most important roles in this context. In recent studies, topics such as the synthesis procedures of the Fischer-Tropsch catalytic system and the influence of active metals, promoters and supports on the activity and selectivity have been investigated. However, they are mainly devoted to the selective production of a wide fraction of C5+ hydrocarbons [9]. The catalytic reaction that facilitates the conversion of syngas to branched-chain hydrocarbons, notably isobutane and isobutene, is referred to as “isosynthesis” [10]. This reaction provides a promising approach for producing isobutene and isobutane by selectively transforming syngas, a mixture of carbon monoxide (CO) and hydrogen (H2). Typically, syngas are derived through gasification and can be generated from various sources, such as natural gas, coal, and biomass, by reacting these feedstocks with steam or oxygen. Compared to conventional petroleum cracking, isosynthesis presents advantages, primarily due to the abundant availability of coal and natural gas as alternative raw materials [11]. The main production method of isobutene, which is in the light olefin group, is the cracking of naphtha, a petroleum product, with water vapor [12]. This method has disadvantages, such as consuming large amounts of energy and releasing harmful emissions [13]. In addition to these disadvantages, the increase in oil prices due to the limited oil reserves worldwide has led researchers to seek an alternative source [11]. Synthesis gas is more advantageous than petroleum and its derivatives in terms of being a renewable resource [10]. For this reason, interest in synthesis gas, which is an alternative source that can be used in isobutene production, has increased in recent years [1, 2, 14-16]. The catalytic reaction that selectively converts the synthesis gas, which is a mixture of CO and H2, into isobutene and isobutane is called isosynthesis [17-20]. Isosynthesis reactions are as follows [1]:
4CO + 8H2 → i-C4H8 + 4H2O ΔHr=-542 kJ/mol
4CO + 9H2 → i-C4H10 + 4H2O ΔHr=-659 kJ/mol
This reaction, also known as CO hydrogenation, is a part of the Fischer-Tropsch reaction mechanism [21]. It is assumed that after the initial activation of both H2 and CO on the suitable catalyst surface, a gradual carbon chain growth follows [15, 16]. The main purpose of the process is to maximize low olefin selectivity, reduce methane production, and prevent excessive CO2 formation [22].
There are many studies in the literature, including thermodynamic analysis of isosynthesis [14, 20, 22-27]. Neto and Schmal aimed to investigate the isosynthesis reaction on Ce-based nanocatalysts. In this study, it was observed that CO conversion and hydrocarbon formation increased with temperature while CO2 formation decreased it. It was found that the selectivity of isobutane and methane increased with temperature, but the selectivity of C5+ and isobutene decreased with temperature [23]. Bi and Dalai investigated the selective formation of C4 hydrocarbons from synthesis gas using Fe-Co/ZrO2 and SO42–/ZrO2 catalysts. In the study, it was observed that CO conversion and total hydrocarbon selectivity increased with temperature in the range of 240-260oC. Still, CO conversion and total hydrocarbon selectivity decreased with temperature in the range of 260-270oC. 260oC was determined as the optimum temperature for C4 hydrocarbon production and CO conversion [24]. Zhu and He investigated the formation of iso-C4 products by CO hydrogenation over CeO2-TiO2 catalysts. In the study, it was observed that CO conversion and hydrocarbon selectivity increased with temperature and pressure. The value of 698 K was evaluated as the optimum temperature and it was stated that iso-C4 selectivity was maximum and C1-C3 selectivity was minimum at this temperature. It was shown that temperature values above the optimum temperature would be thermodynamically disadvantageous. In the same study, the pressure at which i-C4 selectivity was highest was evaluated as 3 MPa [20]. Li et al. aimed to investigate the effect of calcium salt addition to ZrO2 catalyst on isosynthesis. In the study, it was stated that as the temperature increased, the CO conversion increased, but, unlike the literature, the total hydrocarbon formation decreased with the increase in pressure [18]. Li et al. aimed at direct synthesis of isobutane over CuZnZrAl/Pd-b hybrid catalyst using synthesis gas or CO2. It was observed that when the temperature was increased from 260 °C to 290 °C, the synthesis gas conversion increased and the hydrocarbon selectivity was affected. It was stated that the C4 hydrocarbon selectivity increased from 80.2% to 83.8% with the increase of the reaction pressure from 1.5 MPa to 2.5 MPa [25]. Li et al. investigated the selective formation of isobutene by CO hydrogenation over a zirconium dioxide catalyst. It has been reported in the literature that increasing the pressure may cause the product distribution to contain more heavy hydrocarbons, but in this study, the amount of C5+ hydrocarbons decreased considerably. It was observed that increasing the temperature increased the CO conversion and the selectivity of C1-C3 hydrocarbons. It was stated that the selectivity of isobutene among the total hydrocarbons was 32% [26]. Li et al. investigated the effect of CO2 in the feed on isosynthesis using a Zr-based catalyst. In the study, it was observed that CO conversion increased with temperature, but the selectivity of i-C4 among total hydrocarbons decreased. In addition, it was stated that when CO2 was added to the feed, the selectivity of i-C4 among total hydrocarbons decreased at higher temperatures [11]. Erkey et al. studied the production of isobutylene from synthesis gas using zirconia in a suspension reactor (slurry reactor). In the study, it was observed that CO conversions at CO/H2 ratios of 1, 1.5, and 2 at 406 °C and 60 atm were 10%, 11%, and 10% respectively. The selectivities for C4 hydrocarbons were found to be slightly higher when the CO and H2 ratios were 1.5. Among C4 hydrocarbons, isobutylene was observed to be higher in mass percent at all CO/H2 ratios and more than 60% isobutylene selectivity was observed when the CO/H2 ratio was equal [27].
Researchers have used Gaseq, MATLAB, Java, Aspen, and similar auxiliary programs with certain methods while performing thermodynamic analysis [28-36]. Yarbas and Ayas performed a thermodynamic analysis of methane production by low-pressure CO2 hydrogenation. In the study, equilibrium constant, Gibbs free energy, and reaction enthalpies were calculated using Gaseq and MATLAB programs. It was emphasized that the Gibbs free energy minimization method and the use of the Gaseq program were effective in similar thermodynamic analyses [28]. Yilmaz et al. tested the Gibbs energy minimization method in the Java program and also used the MATLAB program to determine the equilibrium conversions [29]. Wang et al. performed regression on the kinetic model with the experimental data collected to estimate the relevant parameters using the Runge-Kutta method on the MATLAB [30]. Another program that can be used for thermodynamic analysis is Aspen Plus. He et al. performed a thermodynamic analysis of the formation of C2-4OH alcohols by hydrogenation of CO2. The thermodynamic effects of various alcohol isomers and methane were shown using Aspen Plus V11 [31]. Ahmad and Upadhyayula performed a thermodynamic analysis of fuel production by CO2 hydrogenation. The Gibbs free energy minimization technique and the Aspen Plus program were used [32]. Iyer et al. aimed to investigate the thermodynamic effect of feed composition on methanol synthesis. For this purpose, Gibbs's free energy minimization technique and the Aspen Plus program were used [33]. Vita et al. performed a thermodynamic analysis with PRO\II (v.8.3) process simulator software to compare biogas reforming processes, steam reforming, and oxy-steam reforming [34]. Nadimpalli et al. aimed to analyze the thermodynamics of the hydrothermal synthesis of nanoparticles. The thermodynamic modeling performed in the study was implemented in Thermo-Calc software and tested with published experimental data for AlOOH (boehmite) [35]. Zhang et al. investigated the thermodynamics of CH3COOH synthesis from CH4 and CO2 using HSC Chemistry 6.0 software and density functional theory [36].
In this study, the first thermodynamic analysis study was carried out for the reaction of synthesis gas to isobutene. Calculations were performed with the traditional stoichiometric method, and the MATLAB program (Mathworks MATLAB R2022) was used in the solution of the equations. The effects of feed composition, temperature, and pressure on CO conversion and isobutene yields were investigated.
2. MATERIALS AND METHODS
2.1. Calculation of Reaction Equilibrium Constants
It is stated that the following reactions may occur for CO hydrogenation [20].
![]() |
(a) |
![]() |
(b) |
![]() |
(c) |
![]() |
(d) |
![]() |
(e) |
![]() |
(f) |
Which of these reaction mechanisms will occur depends on the experimental conditions and the catalyst used [25, 28]. One of the products is the reactant for the other, creating a strong driving force for the overall reaction and allowing very high syngas conversion in one go [25]. In this study, thermodynamic analyses were
Component | ax103 | bx105 | cx108 | dx1012 |
---|---|---|---|---|
Isobutene (i-C4H8) | 82.88 | 25.64 | -17.27 | 50.50 |
Hydrogene (H2) | 28.84 | 0.00765 | 0.3288 | -0.8698 |
Carbon monoxide (CO) | -28.95 | 0.4110 | 0.3548 | -2.220 |
Water (H2O) | 33.46 | 0.6880 | 0.7604 | -3.593 |
carried out using the traditional stoichiometric method by considering the (a) mechanism, which involves direct isobutene production. The reaction is an exothermic reaction. As the temperature increases, the reaction rate increases, but the equilibrium constant decreases. For this reason, temperature is critical to the equilibrium conversions. The decrease in volume observed from the reaction stoichiometry indicates that pressure will have effects on the equilibrium conversions and yields.
Enthalpy and Gibbs free energy values of the relevant reaction components are given in Table 1, and specific heat capacity values are given in Table 2.
Based on the relevant data, the Gibbs free energy change at 25oC was calculated as ΔGo rxn = −307, 52
the enthalpy change, ΔHo rxn = −542, 8
and the equilibrium constant K298= 8.07E+53 using Eq. 1-3. The negative sign of ΔHo rxn indicates that the reaction is exothermic. The negative value of ΔGo rxn indicates that the reaction is spontaneous and there is no thermodynamic equilibrium limitation [28].
![]() |
(1) |
![]() |
(2) |
![]() |
(3) |
In order to calculate the enthalpy change depending on temperature, first, the specific heat change (Eq.4) was determined, and then the expressions giving the change of enthalpy and equilibrium constant with temperature were obtained (Eq.5-6).
![]() |
(4) |
![]() |
(5) |
![]() |
(6) |
(Fig. 1) shows the change of lnK with temperature.
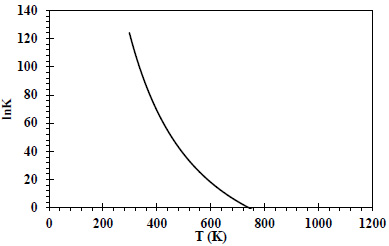
(Fig. 1) shows that lnK values decrease with temperature. Positive lnK values were detected for temperatures between 300-740K. It is seen that the potential for the reaction to occur is highest in the relevant temperature range [28]. Feng (1994) investigated the selective formation of isobutane and isobutene from synthesis gas on zirconia catalysts. Different reactions where different products could be formed were mentioned. Thermodynamic analysis was performed on the system formed by these different reactions, and it was observed that methanation was thermodynamically more favorable than other reactions [39]. Postula (1994) conducted a thermodynamic analysis of the conversion of synthesis gas to isobutene using precipitated zirconia-based catalysts. His work was based on a few-step reaction system, similar to Feng's work, and it was once again shown that methanation was thermodynamically more favorable [40]. In this study, the lnK-T graph created for the single-step production of isobutene from synthesis gas is consistent with the studies conducted in the literature in terms of its behavior in the temperature range of 300-800K.
2.2. Calculation of Equilibrium Conversions and Yields
Thermodynamics gives the heat liberated or absorbed for a given extent of reaction and the maximum possible conversion. The heat absorbed during the isosynthesis reaction depends on the nature of the reacting system, the amount of material reacting, and the temperature and pressure of the reacting system and is calculated from the heat of the reaction. The heat of reaction at temperature T2, knowing the heat of reaction at temperature T1, is found by the law of conservation of energy. Knowing the heat of reaction at any one temperature, as well as the specific heat of reactants and products in the temperature range concerned, allows us to calculate the heat of reaction at any other temperature. From this, the heat effects of the reaction can be found. From the second law of thermodynamics, equilibrium constants, hence equilibrium compositions of reacting systems, can be calculated. For gas reactions, standard states are usually chosen at a pressure of 1 atm. At this low pressure, the deviation from ideality invariably is small; hence, fugacity and pressure are identical. The equilibrium composition, as governed by the equilibrium constant, changes with temperature, and from thermodynamics, the rate of change is given by Van’t Hoff Equation [41].
Thermodynamic models were conducted at different feed compositions, pressures and temperatures. The pressures P= 1 atm, 5 atm, 10 atm, 30 atm, and 50 atm representing low, medium and high pressures and the temperature range T=400-1000K were studied. The pressure applied in the reaction affects the activity of the catalyst. The pressure range of 0.1 - 5.0 MPa is preferred [42]. In previous studies, the effect of H2-rich feed composition has been analyzed. It has been suggested that excess H2 in H2-rich feed may increase the formation of methane and C4 hydrocarbon products by encouraging Ci intermediate species to hydrogenate. The highest CO conversion and iC4 selectivity could be obtained when CO/H2=0.3 [39]. In this study, it is envisaged to contribute to reaction studies by analyzing the situation where H2 is limiting. To determine the critical role of H2, three different feed compositions were considered, presented below, where H2 was the limiting reactant:
Case 1: 50%CO+ 50%H2
Case 2: 60%CO+ 40%H2
Case 3: 70%CO+ 30% H2
The equilibrium constant is unaffected by the pressure of the system or by the kinetics of the reaction but is affected by the temperature of the system. Though the thermodynamic equilibrium constant is unaffected by pressure, the equilibrium concentration of materials and equilibrium conversion of reactants can be influenced by pressure [41]. The equations giving the relationship between the equilibrium constant, Kp, and the equilibrium conversions, x, considered in the calculations are given in Table 3.
Case | Kp |
---|---|
Case 1: 50%CO+ 50%H2 |
![]() |
Case 2: 60%CO+ 40%H2 |
![]() |
Case 3: 70%CO+ 30% H2 |
![]() |
![]() |
(7) |
![]() |
(8) |
![]() |
(9) |
![]() |
(10) |
Ky is the mole fraction constant, yi is the mole fraction, and Δγ shows the change in stoichiometric coefficients Eqs. 7-10.
MATLAB is a computer program generally used for positive science and engineering calculations. Developed by the United States-based MathWorks company, MATLAB is also a programming language. As its name suggests, MATLAB has a matrix-based working system. The MATLAB program, which allows many mathematical calculations such as linear algebra, statistics, optimization, numerical analysis, and Fourier analysis to be done effectively and quickly, is also used for 2D and 3D graphic drawing.
In the calculation of equilibrium compositions, Fzero command of MATLAB was used in solving the equation set. This command finds the roots of nonlinear functions around a given initial estimate using an algorithm consisting of a combination of bisection, secant and inverse quadratic interpolation methods [43]. Considering the complexity of the equation and the possibility of multiple roots, 200 different starting points with equal intervals between -5 and 5 were determined. The equation was equated to KT values for all temperatures, ensuring that all possible roots were found. Using these composition values, CO conversion, isobutene selectivity, and isobutene yields were calculated. Eqs. 11-13 were used in the calculations of CO equilibrium conversion, isobutene equilibrium selectivity, and yield, respectively.
![]() |
(11) |
![]() |
(12) |
![]() |
(13) |
3. RESULTS AND DISCUSSIONS
3.1. Case 1: Equilibrium Conversions and Yields
CO conversions obtained at different pressures and temperatures for the feed containing 50% CO and 50% H2 are given in Fig. (2), and isobutene yields are given in Fig. (3).
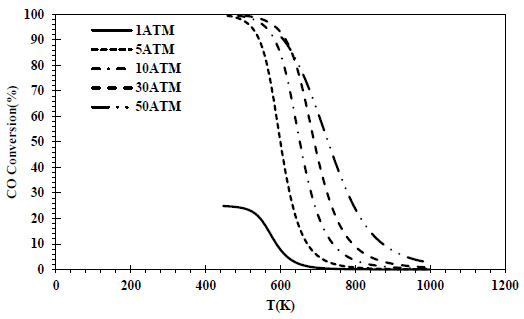
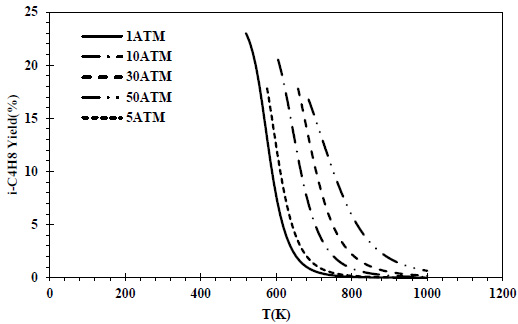
In the thermodynamic analysis of equal volume feed composition, the maximum CO conversion achieved at pressures other than atmospheric pressure is the same. However, as the pressure increases, the temperature at which the maximum conversion value is observed also increases. While the maximum equilibrium conversion (25%) at 1 atm is obtained at 452 K, the same conversion value is reached at 796 K and 50 atm. According to the stoichiometry of the CO hydrogenation reaction, H2/CO should be 2. When the feed ratio is lower than the stoichiometry (H2/CO= 1), the CO conversion decreases significantly. It is seen that this effect is eliminated in high-pressure (>5atm) operation. However, high pressures depending on the catalyst used give different effects. At 60 atm, only 10% CO conversion was achieved [27].
The maximum isobutene yield value at atmospheric pressure was determined as 23% in the relevant composition. The decreasing behavior as the temperature increased, which was determined in the CO conversion values, was also observed in the isobutene yields. The maximum isobutene yield values (>17%) decreased as the pressure increased. Although it varies according to the catalyst, it is stated that the olefin yield decreases as the reaction pressure increases [42]. At the same temperature, higher isobutene yields were determined as the pressure increased. While there was a yield of 0.2 at 5 atm at 800K, approximately 7% yield was obtained at the same temperature at 50 atm.
3.2. Case 2: Equilibrium Conversions and Yields
CO conversions obtained at different pressures and temperatures for the feed containing 60% CO and 40% H2 are given in Fig. (4), and isobutene yields are given in Fig. (5).
In the relevant feed composition, the lowest CO conversions (45%) were obtained at atmospheric pressure. As the pressure increased, the equilibrium conversions increased, and the maximum conversion value of ⁓94% was reached at 50 atm pressure. With the increase of pressure, the reaction shifts to the side where the number of moles is less. Thus, when the pressure on this reaction is increased, or the volume of the system is reduced, the reaction will shift to the direction that will reduce this external effect. As expected, the conversions increased as the pressure increased. At 1 atm pressure, only 30-45% conversions were achieved.
Isobutene yield values exhibited similar behavior as observed in CO conversion. The lowest yield values were reached at atmospheric pressure, and isobutene yields increased with increasing pressure. 23% isobutene yield was obtained at 50 atm and 430 K.
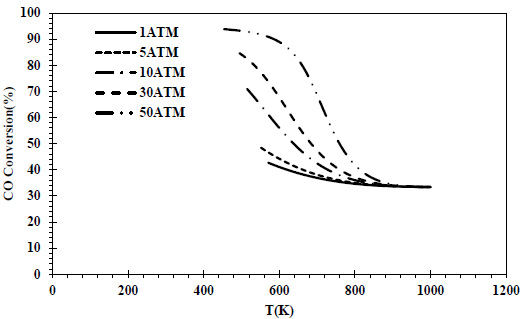
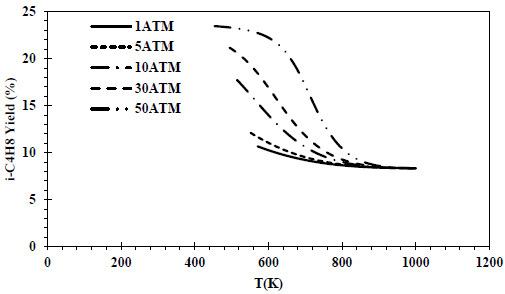
3.3. Case 3: Equilibrium Conversions and Yields
CO conversions obtained at different pressures and temperatures for the feed containing 70% CO and 30% H2 are given in Fig. (6), and isobutene yields are given in Fig. (7).
In the CO-rich feed composition where H2 was again the limiting reactant, the same maximum CO conversion value (20%) was reached at all pressures. The conversion values decreased with temperature at each pressure.
In the relevant composition, the same maximum isobutene yield (5%) was reached at all pressures. As the pressure increased at the same temperature, the isobutene yield values increased.

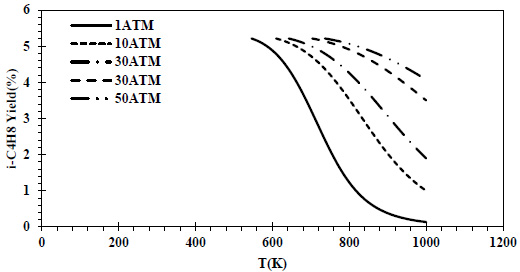
In all thermodynamic models, it was observed that the equilibrium conversion values of the exothermic reaction of isobutene production from synthesis gas decreased with temperature [20, 23, 24]. In Zr-based catalysts, a temperature range of 673-723K is recommended for this reaction [22]. Increasing the CO composition in the feed composition led to a decrease in CO conversions and isobutene yields. This decrease reached a serious level (⁓4 times) at 70% CO content. In all feed compositions, isobutene yields of one-fourth of the conversions were obtained due to the reaction stoichiometry. Isobutene selectivity was 25% regardless of feed composition, temperature and pressure. Similar selectivities are reported in the literature [28]. As a result of thermodynamic modeling, the reaction proceeding over the feed with equal volume composition will provide higher yields and CO conversions. In this composition, it is recommended to operate at a minimum pressure of 5 atm and 460K. In the literature, optimum temperatures for the reaction are recommended as greater than 500K [20, 24]. The reduction of the H2 in the feed composition has a negative effect on both CO conversions and isobutene yields. A 50% H2 content can be considered the most suitable composition in three different component compositions where H2 is the limiting reactant. The syngas composition can vary considerably depending on the feedstock and the gasification process involved but typically consists of 30–60% carbon monoxide (CO), 25–30% hydrogen (H2), 0–5% methane (CH4), 5–15% carbon dioxide (CO2), small amounts of water vapor, hydrogen sulfide (H2S), carbonyl sulfide (COS), and some ammonia and other trace pollutants [44]. It also seems possible to provide a natural feed source containing CO and H2 with a similar volumetric composition.
Isosynthesis provides a promising approach for producing isobutene and isobutane by selectively transforming syngas, a mixture of carbon monoxide (CO) and hydrogen (H2). Typically, syngas are derived through gasification and can be generated from various sources, such as natural gas, coal, and biomass, by reacting these feedstocks with steam or oxygen [11]. The fact that many countries are dependent on oil has led to the search for alternative resources that can be used other than oil. Another factor that encourages this search is the increase in social awareness and the desire to reduce CO2 emissions. Steam-cracking is still the primary method for olefin synthesis, but it is endothermic; therefore, extremely high temperatures are needed to obtain light olefins [45]. Despite the improvements made in the steam cracking process, it is considered one of the most energy-consuming technologies in the petrochemical industry and results in high CO2 emissions. Some 40% of the total annual energy consumption in petrochemical plants is due to steam cracking [46]. Additionally, selectivity for light olefins in steam cracking is difficult to control.
The interaction between transfer processes and chemical kinetics, the basis of physicochemical hydrodynamics, is a major concern of chemical reaction engineering. Another area of great use in reaction engineering and catalyst development is the elucidation of how thermodynamic constraints drive the development of catalysts and the design of chemical reactors. This is particularly important today because thermal efficiency has much significance in the process industries due to recent changes in the cost of natural gas and oil. The constraints that determine thermal efficiency in a chemical process are examined. It is seen that the constraints that limit efficiency are not inherent thermodynamic constraints but rather are the result of limitations of existing catalysts and technologies. It is important to evaluate these constraints and the opportunities for improvement.
CONCLUSION
Thermodynamic analysis was performed for the reaction of isobutene production from synthesis gas. The effects of feed composition, temperature (400-1000K), and pressure (1atm, 5atm, 10atm, 30atm, 50atm) on CO conversion and isobutene yields were investigated. In order to analyze the effect of feed composition and to reveal its critical role, thermodynamic models were conducted in three different compositions (Case 1-3) where H2 was the limiting reactant. It was observed that CO conversions decreased as temperature increased in all feed composition and pressure operations for the isosynthesis reaction, which is an exothermic reaction. Similar behavior was also observed for isobutene yields. It was shown that increasing the H2 content in the feed composition increased the CO conversion and isobutene yields. It was determined that a feed composition with equal volumes of CO and H2 content could give high CO conversions (>90%) and isobutene yields (⁓25%) at a relatively low pressure of 5 atm. Climate change affects areas such as water resources, natural disasters, biodiversity, ecosystem services and public health, which are directly related to social and economic sectors and living things. In this process, the conversion of emissions into olefins can make significant contributions to the carbon footprint and the climate change process. It is expected that the study will provide important inputs to critical isosynthesis reaction applications.
AUTHORS CONTRIBUTIONS
It is hereby acknowledged that all authors have accepted responsibility for the manuscript's content and consented to its submission. They have meticulously reviewed all results and unanimously approved the final version of the manuscript.
LIST OF ABBREVIATIONS
FCC | = Fluid catalytic cracking |
MTO | = Methanol-toolefins |
AVAILABILITY OF DATA AND MATERIALS
The data and supportive information are available within the article.
ACKNOWLEDGEMENTS
Declared none.