All published articles of this journal are available on ScienceDirect.
Study on the Purification Process of Phosphoric Acid Using Organic Solvents: A Case of Wet-process Phosphoric Acid Based On Karatau Phosphorites
Abstract
Introduction
This article presents research data on the processes used to produce concentrated phosphoric acid from Karatau phosphate rock.
Methods
The study investigated the purification of wet-process phosphoric acid using liquid-liquid extraction with organic solvents. To determine the composition of extractable complexes formed during the extraction of phosphoric acid with tributyl phosphate and n-butyl alcohol, infrared spectroscopy was employed. In addition, physicochemical transformations under thermal exposure were analyzed using differential thermal analysis.
Results
The effect of magnesium salts and sulfuric acid impurities on the distribution factor of phosphoric acid was investigated. Increasing the initial concentration of phosphoric acid from 5.38% to 25.61% P2O5 at 25°C led to an increase in the distribution factor from 0.178 to 0.436 for n-butyl alcohol, from 0.06 to 0.183 for isoamyl alcohol, and from 0.120 to 0.320 for tributyl phosphate. Increasing the temperature from 25°C to 60°C had little to no impact on the distribution factor. The results showed that the distribution factors of phosphoric acid are influenced by its initial concentration, particularly in the presence of sulfuric acid. Among the solvents tested, n-butanol demonstrated the highest extraction efficiency. The phosphoric acid concentration was increased to 56%–63% P2O5, with sulfuric acid impurity levels reduced to ≤ 0.002%.
Discussion
The results of the study demonstrate a significant contribution to the field of optimizing phosphoric acid extraction using organic solvents. One of the innovative aspects of the work is the analysis of extraction mechanisms using various solvents, including n-butanol, tributyl phosphate, and isoamyl phosphate. This contribution significantly expands the scientific understanding of extraction processes and opens up new possibilities for optimizing phosphoric acid purification technology.
Conclusion
For the first time, countercurrent extraction and azeotropic distillation were combined to address the issue of equipment corrosion caused by fluorine impurities. The findings of this study can be applied in developing a fundamental technological process for the deep purification of technical-grade phosphoric acid, resulting in the production of pure and highly concentrated phosphoric acid.
1. INTRODUCTION
Mineral fertilizer companies in Central Asia and Kazakhstan utilize phosphorites from the Karatau phosphate deposit as their primary phosphate raw material [1-8].
Phosphoric acid serves as the foundation for the production of concentrated phosphate fertilizers [9-11]. Currently, the most cost-effective method for its production is the sulfuric acid process, which involves the decomposition of phosphate raw materials. When applied to Karatau phosphorite, this method yields phosphoric acid with a relatively low P2O5 content (18%–20%) and a high level of impurities, including magnesium, iron, and aluminum salts. The quantity and composition of these impurities depend on both the quality of the raw phosphate and the specific extraction method used. The total impurity content can reach up to 15 mass percent. The main impurities include fluoride and sulfate ions, as well as cations of iron, aluminum, calcium, magnesium, sodium, and potassium. In phosphoric acid, fluoride compounds are present as hydrofluoric and silicofluoric acids, as well as in complex forms with phosphoric acid, aluminum, and iron [12-19].
Attempts to increase the concentration of phosphoric acid by improving the production technology or through evaporation have not yielded positive results. As the acid concentration increases, its viscosity also rises, disrupting the filtration process and causing precipitation during evaporation [20].
Current trends in wet-process phosphoric acid production focus on modernization and the development of advanced purification methods, such as liquid-liquid extraction using organic solvents [21-23]. A key aspect of these methods is the selection of organic extractants with high distribution factors. However, relatively few studies have explored phosphoric acid extraction using solvents. Among the most commonly used extractants for removing metal cations and fluorine from wet-process phosphoric acid are n-butanol, isobutanol, and isoamyl alcohol [24, 25].
The molecular structure of a solvent plays a crucial role in its ability to form soluble complexes with phosphoric acid and its impurities. For instance, n-butanol contains a hydroxyl group (–OH) that can form hydrogen bonds with phosphoric acid molecules, aiding in the transfer of phosphoric acid into the organic phase. Moreover, the spatial arrangement of the –OH group enables it to act both as a hydrogen bond donor and acceptor. As a result, alcohols can solvate both cations and anions during the extraction of inorganic acids. Consequently, water-soluble alcohols are particularly effective for purifying phosphoric acid via solvent extraction.
Isoamyl alcohol, by contrast, has a lower polarity, which may reduce its effectiveness in extracting phosphoric acid from low-concentration systems. However, it can be more efficient in high-concentration systems, where interactions between the solvent and acid molecules are more pronounced.
Glacial acetic acid mainly forms insoluble salts with iron and aluminum, and various extraction methods are employed using solvents that are immiscible or partially miscible with water. Another approach involves reducing the solubility of contaminant salts by adding organic solvents that are fully miscible with water. However, these industrial methods are not universal, as they typically require specific chemical reagents to target each impurity. Despite the high associated costs, these methods can achieve a purification level of approximately 0.05–0.01 wt.% for each impurity component.
Organic solvents immiscible with water are commonly used as extractants. Tributyl phosphate (С4Н9)3РО4 exhibits high selectivity for phosphoric acid. However, the high cost of tributyl phosphate makes the process expensive, highlighting the need to explore alternative, more cost-effective extractants.
Benzene and ethyl acetate are widely used organic solvents with strong extraction properties. However, benzene is highly toxic and carcinogenic, and as a non-polar solvent, its use for extracting polar substances, such as phosphoric acid, is limited. While ethyl acetate is polar, it may be less effective in extracting phosphoric acid compared with more specialized solvents.
Aldehydes and ketones, such as alcohols, contain oxygen atoms, which impart basic properties to the molecule due to the presence of a lone pair of electrons on the oxygen atom. This enables the formation of donor-acceptor bonds. However, aldehydes and ketones have a weaker ability to solvate compared with alcohols, making it more difficult for them to transfer highly hydrated phosphoric acid from an aqueous solution into an organic solvent. This explains why aldehydes and ketones have weaker extraction properties than alcohols. On the other hand, isoamyl alcohol molecules have a simpler structure than tributyl phosphate and n-butanol, which may limit their ability to form stable complexes with phosphoric acid, especially in the presence of impurities.
As organic solvents, n-butanol, isoamyl alcohol, and tributyl phosphate are widely recommended for purifying phosphoric acid from impurities.
A method for purifying extracted phosphoric acid using a mixture of organic solvents, diisopropyl ether, and tri-n-butyl phosphate has been presented [26]. However, the method is complex, and the frequency of its process is a significant drawback.
Another method for producing purified phosphoric acid involves the preliminary preparation of extracted phosphoric acid, followed by extraction with tributyl phosphate in the presence of sulfuric acid. The organic phase is then washed with a portion of the re-extract, and the phosphoric acid is re-extracted into the aqueous phase. A portion of the re-extract is recycled back into the process [27].
Raw Material – Karatau Phosphorite | Content, Mas. % | |||||||
---|---|---|---|---|---|---|---|---|
Р2О5 | К2О | СаО | MgO | R2O3 | F | SO3 | insoluble residue | |
26,81 | 41,68 | 1,96 | 0,79 | 17,05 | ||||
Phosphoric acid | 25 | 20,58 | - | 2,87 | 1,17 | 1,51 | 3,64 | - |
However, this method has several drawbacks: its periodic nature, the production of relatively diluted acid, and the need for additional reagents (Na2S, H2S) for impurity extraction. Moreover, the high cost of TBP renders the process economically unfeasible. TBP is an expensive reagent with high density in saturated extracts, similar to water, which negatively impacts the hydrodynamics of the extraction process. This results in the formation of emulsions and longer phase separation times. Additionally, TBP is soluble in acidic aqueous solutions, chemically unstable, and prone to hydrolysis and decomposition in strongly acidic media.
Research focused on optimizing the extraction of phosphoric acid using organic solvents and obtaining concentrated phosphoric acid through liquid extraction methods is both innovative and highly relevant for practical applications in chemical production.
By decomposing raw phosphate materials with concentrated sulfuric acid, followed by heating the mixture and extracting with organic solvents, it is possible to achieve a high yield of P2O5 in phosphoric acid production [28].
The dehydration of pure phosphoric acid has been extensively studied across a wide temperature range [29, 30]. It has been shown that the composition of the dehydration products depends on the amount of P2O5 present.
The dehydration of wet-process phosphoric acid [31-33] in the presence of impurities (R2O3, F) differs from that of pure phosphoric acid. Polymorphs form at lower temperatures, and their content is higher than in the dehydration products of pure phosphoric acid, even when the total P2O5 content is the same. Impurities generally increase the viscosity of the acid, and the presence of aluminum ions results in the formation of aluminum tripolyphosphate. No data have been found on the dehydration of phosphoric acid in the presence of sulfuric acid. However, patent references suggest that small amounts of H2SO3 during the dehydration of phosphoric acid lead to the formation of ultrasulfophosphoric acid [34].
Thus, research aimed at identifying optimal and effective methods for purifying wet-process phosphoric acid is crucial. The objective of this study is to obtain concentrated phosphoric acid from wet-process phosphoric acid through liquid extraction using organic solvents. Additionally, the study examines the impact of sulfuric acid concentration in the mixture on the dehydration process of phosphoric acid.
2. MATERIALS AND METHODS
Karatau phosphorite, a natural mineral composed of calcium phosphates, was used in this study. Wet-process phosphoric acid, produced via the dihydrate method from Karatau phosphorite (Table 1), served as the subject of analysis. The phosphoric acid concentration was 25% by P2O5, and the process was carried out at a temperature of 25°C. The following reagents were used for analysis: orthophosphoric acid (H3PO4) with 85% purity (concentrated, AR grade), sulfuric acid (H2SO4) with 96% purity (concentrated, AR grade), magnesium sulfate (MgSO4·7H2O) (AR grade), magnesium monophosphate (MgHPO4) (AR grade), butanol (C4H9OH) (AR grade), isoamyl alcohol (C5H12O) (AR grade), and tributyl phosphate (C12H27O4P) (AR grade). All chemicals were purchased from Laborfarma LLP (Kazakhstan) and used without further purification.
To increase the concentration and purify phosphoric acid, liquid extraction with organic solvents was employed [35-39]. The extraction process involves transferring phosphoric acid from aqueous solutions to organic solvents that selectively bind the acid. This method is commonly used in industrial settings, particularly in the chemical and mining industries, to purify and concentrate phosphoric acid.
Phosphoric acid is then washed out of the solvent with water using the counterflow principle. Since technical acid contains free sulfuric acid, various magnesium, iron, and aluminum salts, as well as fluoride (SiF6) as impurities, the distribution of pure phosphoric acid between water and solvents like n-butyl alcohol, isoamyl alcohol, and tributyl phosphate was studied in advance. This study considered factors such as temperature, phosphoric acid concentration, and the concentration of impurities like H2SO4, MgSO4, and Mg(H2PO4) in technical phosphoric acid. Organic solvents, such as n-butanol, isoamyl alcohol, and tributyl phosphate were used for extracting phosphoric acid. The purity of the solvent affected the presence of impurities and the distribution of phosphoric acid between the phases.
The extraction of phosphoric acid was conducted with a volume ratio of phosphoric acid to extractant of 1:1 at a temperature of 25°C, maintained in a water thermostat with an accuracy of ± 0.50°C. Equal volumes of the aqueous and organic phases were placed in separating funnels mounted on a disk in the thermostat. The stirring speed was set between 300 and 500 rpm and continued until equilibrium was reached, which took 15 minutes in these experiments. After stirring, the funnels were left in the thermostat until the phases had completely separated. To determine the acid concentration, samples were taken from both the organic and aqueous phases, diluted with water, and titrated with 0.05N NaOH using phenolphthalein as an indicator. If sulfuric acid was present, titration was performed with both methyl red and phenolphthalein. The distribution factor was calculated as the ratio of the equilibrium concentrations in the organic and aqueous phases, respectively.
In the next series of experiments, the influence of magnesium salts and sulfuric acid, present as impurities in technical phosphoric acid, on the distribution factor of phosphoric acid was investigated. Magnesium sulfate and magnesium monophosphate were used, with concentrations ranging from 0.5% to 2.5% in terms of MgO. The sulfuric acid concentration varied from 0.30% to 6.19% SO3.
Since technical phosphoric acid derived from Karatau phosphorites consistently contains free sulfuric acid and magnesium salts, experiments were conducted to examine the effect of sulfuric acid concentration on the distribution factor of phosphoric acid in the system H3PO4-MgSO4-H2SO4-H2O, using n-butanol, isoamyl alcohol, and tributyl phosphate.
In the subsequent series of experiments, the extraction of technical phosphoric acid, produced by the sulfuric acid decomposition of Karatau phosphorites using the dihydrate method, was studied with n-butyl alcohol.
Phosphoric acid was treated with a specified amount of alcohol in organic solvent-to-acid ratios of 4:1 and 3:1 three or four times until nearly complete extraction of phosphoric acid was achieved. The extract was then used to treat a new portion of phosphoric acid.
The resulting extracts were azeotropically distilled to recover the solvent, with water added in a stoichiometric amount to form an azeotrope with n-butanol. To ensure precise dehydration, it is important to control both the temperature and pressure within the apparatus. The distillation temperature was kept between 45°C–64°C for n-butanol, while the pressure ranged from 410 to 420 mm Hg. The heating rate was gradual, with a controlled temperature increase of 1°C–2°C per minute, to avoid any solvent breakdown or loss of phosphoric acid. To address this issue, K2SO4, MgSO4, and Na2SO4 were added to technical phosphoric acid, with the aim of binding fluorine as insoluble salts such as K2SiF6, Na2SiF6, and MgF6 [40].
The effect of sulfuric acid concentration on the dehydration process of phosphoric acid was also investigated. The dehydration of pure phosphoric acid has been extensively studied across a wide temperature range, revealing that the composition of the dehydration products depends on the P2O5 content. However, the dehydration of phosphoric acid obtained through the wet process, in the presence of impurities, behaves differently from that of pure acid. At lower temperatures, polymorphs form, and their concentration is higher in the dehydration products, even with the same total P2O5 content. Impurities generally increase the viscosity of the acid, and the presence of aluminum ions further influences the process.
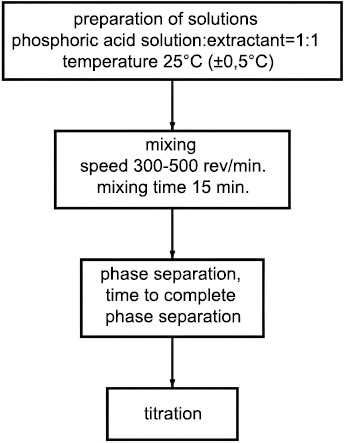
Block diagram of the phosphoric acid extraction process.
The dehydration process of phosphoric acid in the presence of sulfuric acid was investigated over a wide range of ratios and temperatures. Mixtures of sulfuric and phosphoric acids were prepared in the following molar ratios: P2O5:SO3 = 1:1, 1.7, 2.3, 3.3, and 4.4. The experiments were conducted in platinum crucibles, and the initial mixtures were stored in a desiccator. The P2O5 and SO3 content in the samples was determined using standard gravimetric methods. Hydrolysis of polyforms was prevented by adding cold alkali, and the qualitative composition of the products was analyzed through paper chromatography [41].
Thermograms of the initial mixtures were obtained using the SDTQ600 thermal analyzer. This device allows for the simultaneous recording of changes in sample mass (thermogravimetric analysis) and processes associated with heat release or absorption (differential scanning calorimetry/differential thermal analysis) [42].
The mixtures were heated from 100°C to 300°C in an oven for 4 hours, with the temperature maintained to an accuracy of ±5°C. After heating, the acid mixtures varied in consistency, ranging from syrupy to solidifying into a firm mass.The flowchart of the extraction process is illustrated in Fig. (1).
To determine the composition of the complexes formed during the extraction of phosphoric acid with tributyl phosphate and n-butyl alcohol (hereafter referred to as n-BA), an infrared (IR) spectroscopic study was conducted on the extracts in the systems tributyl phosphate - H3PO4 - H2O and n-butyl alcohol - H3PO4 - H2O. The concentration of phosphoric acid in the extracts ranged from 0.15 to 4.15 mol/L for the tributyl phosphate system and from 0.0341 to 1.56 mol/L for the n-butyl alcohol system.
3. RESULTS AND DISCUSSION
The extraction of phosphoric acid from its solutions involves transferring phosphoric acid to the organic phase, while impurities remain in the aqueous phase. Various compounds can serve as extractants, including aliphatic and cyclic alcohols, alkyl phosphates, ketones, aldehydes, ethers, and esters. A thorough theoretical analysis of extraction efficiency using different organic solvents considers key factors, such as solvent polarity, molecular structure, and the specific interactions between the solvent and phosphoric acid components. These parameters influence the extraction mechanism and ultimately determine the process's efficiency.
Polar solvents generally interact more effectively with ionic compounds, such as phosphoric acid, which is a polar substance. However, when extracting phosphoric acid from solutions containing impurities, such as metal salts, it is important to consider not only the polarity of the solvent but also its ability to dissolve both the acids and the impurities.
The results of the distribution of phosphoric acid as a function of its initial concentration are illustrated in Fig. (2).
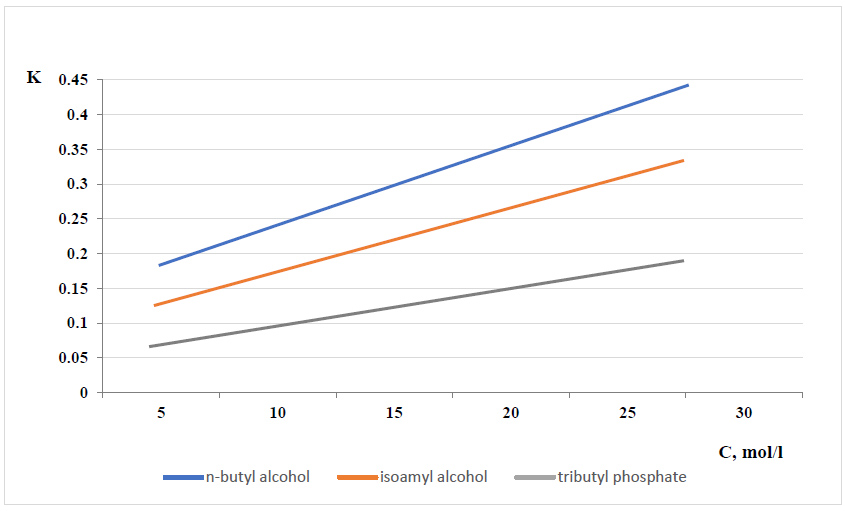
Dependence of the distribution factor (K=Corg./Caqe.) on the initial concentration of phosphoric acid at 25°C.
As illustrated in Fig. (2), an increase in the initial concentration of phosphoric acid (from 5.38% to 25.61% P2O5) leads to a higher distribution factor (K=Corg./Caqe) at 25°C. The distribution factor increases from 0.178 to 0.436 for n-butyl alcohol, from 0.06 to 0.183 for isoamyl alcohol, and from 0.120 to 0.320 for tributyl phosphate.
As the concentration of sulfuric acid increases from 0.30% to 6.19%, the distribution factor of phosphoric acid increases by 1.3 to 1.7 times for all solvents used. The distribution factor of sulfuric acid is highly dependent on its initial concentration, increasing from 0.196 to 0.646 for n-butyl alcohol and from 0.077 to 0.240 for isoamyl alcohol.
During the extraction of phosphoric acid and mixtures of phosphoric and sulfuric acids, an increase in the equilibrium volume of the organic layer is observed for both alcohols and tributyl phosphate.
An increase in temperature from 25°C to 60°C has almost no effect on the distribution factor.
The presence of magnesium sulfate in phosphoric acid, up to 1.05% MgO, also has minimal impact on the distribution factor of phosphoric acid. However, the presence of magnesium monophosphate reduces it by nearly half.
The results of studies determining the effect of sulfuric acid concentration on the phosphoric acid distribution factor in the H3PO4-MgSO4-H2SO4-H2O-n-butanol, isoamyl alcohol, and tributyl phosphate system are summarized in Table 2. A comparison of the data in Tables 2 and 3 shows that the combined presence of magnesium sulfate and sulfuric acid influences the phosphoric acid distribution factor in a manner similar to their individual effects.
MgO Content in the Initial Solution, Mas. % |
n-Butyl Alcohol | Isoamyl Alcohol | Tributyl Phosphate | ||||||
---|---|---|---|---|---|---|---|---|---|
Сorg. | Сaque. | Кd | Сorg. | Сaque. | Кd | Сorg. | Сaque. | Кd | |
% P2О5 |
% P2О5 |
% P2О5 |
% P2О5 |
% P2О5 |
% P2О5 |
||||
MgO in the form of MgSO4 | |||||||||
0,63 | 7,43 | 22,23 | 0,334 | 4,07 | 23,72 | 0,170 | 6,45 | 21,73 | 0,297 |
1,05 | 8,67 | 21,03 | 0,412 | 4,09 | 23,60 | 0,170 | 6,57 | 21,48 | 0,304 |
1,63 | 8,59 | 20,41 | 0,421 | 4,37 | 23,41 | 0,190 | 6,75 | 21,16 | 0,319 |
2,10 | 8,73 | 22,16 | 0,394 | 4,68 | 23,45 | 0,201 | 7,05 | 21,19 | 0,331 |
2,64 | 9,11 | 21,60 | 0,422 | 5,00 | 23,54 | 0,209 | 7,36 | 21,24 | 0,347 |
MgO in the form of Mg(Н2РО4)2 | |||||||||
0,56 | 8,79 | 23,87 | 0,370 | 4,15 | 26,09 | 0,154 | 6,66 | 23,28 | 0,286 |
1,02 | 7,47 | 24,84 | 0,301 | 3,62 | 26,13 | 0,135 | 6,67 | 23,28 | 0,287 |
1,48 | 6,58 | 26,19 | 0,247 | 3,14 | 26,19 | 0,119 | 5,83 | 23,65 | 0,248 |
2,04 | 5,57 | 25,02 | 0,221 | 2,67 | 25,94 | 0,105 | 5,37 | 24,44 | 0,217 |
2,44 | 4,55 | 25,21 | 0,184 | 2,19 | 26,15 | 0,084 | 4,81 | 24,79 | 0,195 |
Known Concentration of SO3, % |
Equilibrium Concentration of Phosphoric Acid, Mass. % P2О5 | Кd | |
---|---|---|---|
Сorg. | Сaque. | ||
n-Butyl alcohol | |||
0,14 | 8,42 | 22,14 | 0,379 |
2,01 | 9,47 | 21,47 | 0,442 |
3,57 | 10,54 | 20,91 | 0,501 |
4,77 | 10,77 | 20,28 | 0,534 |
6,15 | 11,82 | 19,97 | 0,590 |
Isoamyl alcohol | |||
0,13 | 4,78 | 23,14 | 0,204 |
2,02 | 5,82 | 22,98 | 0,251 |
3,57 | 6,85 | 22,65 | 0,301 |
4,75 | 7,37 | 21,89 | 0,335 |
6,12 | 8,19 | 21,60 | 0,378 |
Tributyl phosphate | |||
0,13 | 6,98 | 21,10 | 0,330 |
2,02 | 7,90 | 2,92 | 0,377 |
3,58 | 8,28 | 20,55 | 0,402 |
4,77 | 8,49 | 19,95 | 0,425 |
6,15 | 8,91 | 20,02 | 0,443 |
According to the experiments, the distribution factors of phosphoric acid are highly dependent on its initial concentration, especially in the presence of sulfuric acid. Phosphoric acid is extracted more effectively with n-butanol. At a phosphoric acid concentration of 25% P2O5, with 3.57% SO3 of free sulfuric acid, the distribution factor reaches 0.500.
In this study, the waste aqueous phase contained a gelatinous precipitate consisting of impurities that transferred minimally into the organic phase, primarily phosphates and sulfates of iron, aluminum, and magnesium. The extraction results indicated a limiting concentration of P2O5 in n-butanol, approximately 4.5%–5%, beyond which phosphoric acid was no longer transferred to the butanol. During recycling leaching, performed three times at a 3:1 ratio, the recovery of phosphoric acid relative to the total phosphorus pentoxide content ranged from 72% to 78%.
After azeotropic distillation of the solvent, the concentration of phosphoric acid reached 48%–55% P2O5. The solvent recovery in the laboratory experiments was 86%–90%.
Then, K2SO4, MgSO4, and Na2SO4 were added to the technical phosphoric acid with the aim of binding fluorine in the form of insoluble salts, such as K2SiF6, Na2SiF6, and MgF6. Extraction results showed that the addition of potassium and sodium sulfates effectively bound fluorine into insoluble compounds, preventing its transfer to the organic phase. Furthermore, in the presence of these sulfates, the phosphoric acid recovery factor increased, likely due to the salting-out effect of sulfuric acid generated through exchange reactions between the added sulfates and fluorine-containing acids. As a result, the recovery factor of phosphorus pentoxide in the organic phase increased from 70%–71% (without additives) to 81%–83% (with the addition of potassium and sodium sulfates). Additionally, the free sulfuric acid content in the phosphoric acid rose to 4%–5%.
The phosphoric acid obtained after solvent volatilization contains a high concentration of phosphorus pentoxide, ranging from 56% to 63%. The remaining aqueous phase, after neutralizing the free acid with ammonia or calcium oxide (or calcium carbonate) and drying, can be used as a fertilizer. This is because the P2O5 (20%–25%) content is fully soluble in ammonium citrate.
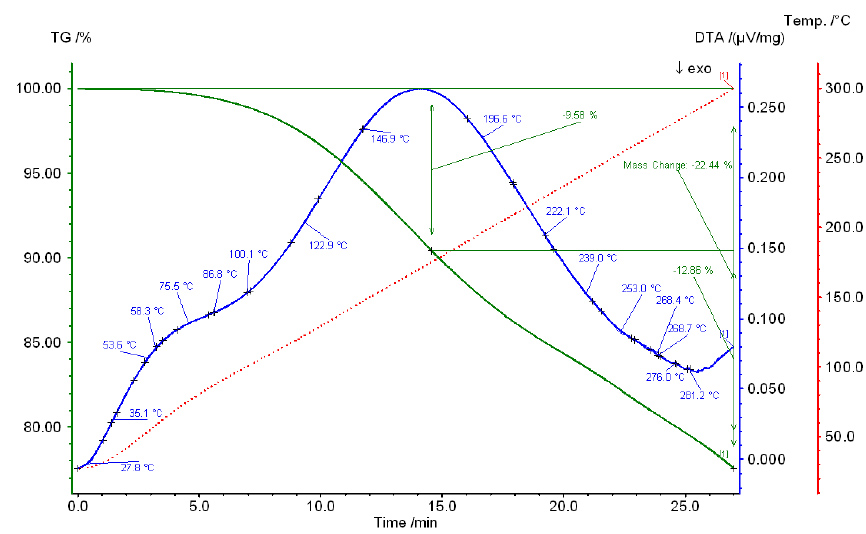
Thermogram of pure phosphoric acid.
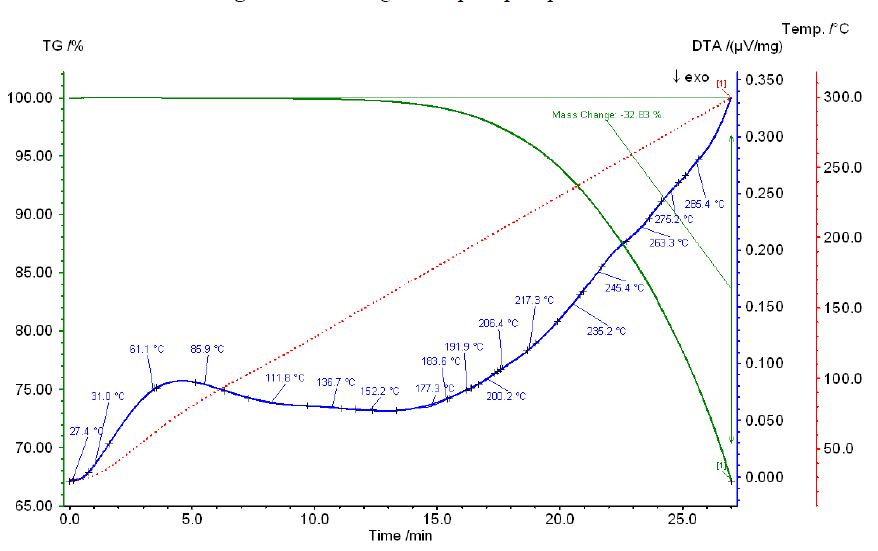
Thermogram of pure sulfuric acid.
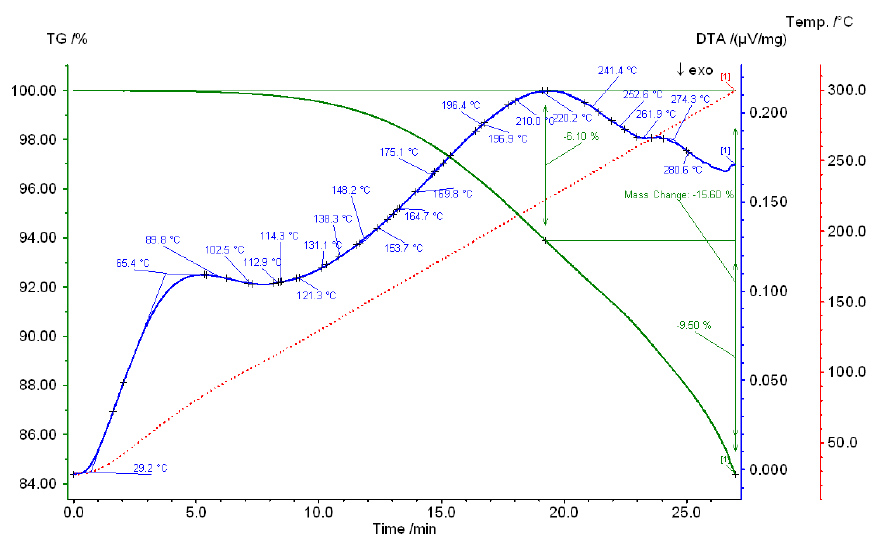
Thermogram of a phosphoric and sulfuric acid mixture with a P2O5:SO3 ratio of 1:1.
Thus, it is demonstrated that the extraction of phosphoric acid from solutions obtained by sulfuric acid decomposition of Karatau phosphorites using n-butanol, based on the counterflow principle, followed by azeotropic volatilization of the solvent, enables the production of highly concentrated phosphoric acid (56%–63% P2O5).
As the temperature increases, the total weight loss increases similarly for all mixtures. With an increase in the amount of SO3 in the mixture, the total loss decreases, but only slightly, reaching 12.33% for mixture V and 9.87%–10.27% for mixtures II-IV. Chemical analysis data show that within the temperature range of 100°C–250°C, no transition from orthoform to pyroform occurs. Starting from 300°C, pyroform appears alongside orthoform in all mixtures, with the amount of pyroform decreasing as the SO3 content in the mixture increases. For example, in mixture I, with 40.96% SO3, the pyroform content is 10.60%, while in mixture IV, with 57.94% SO3, the pyroform content is 0.87%.
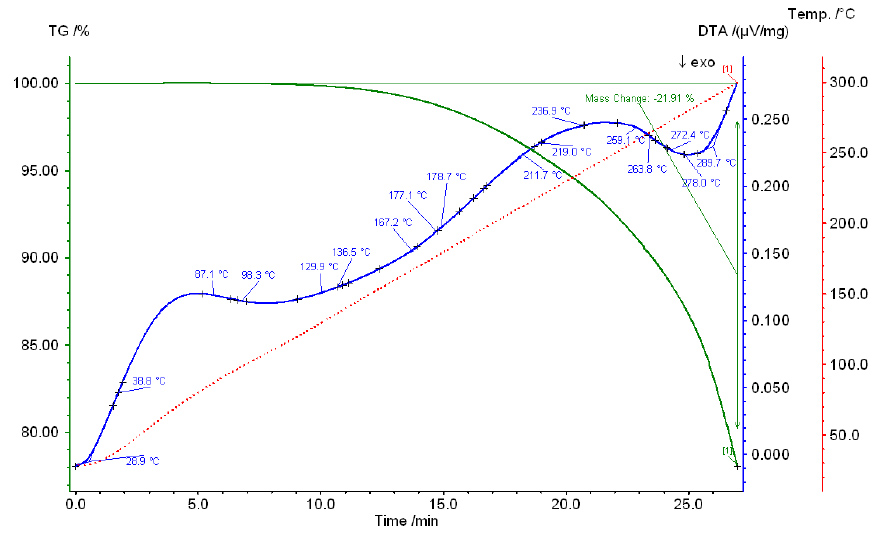
Thermogram of a phosphoric and sulfuric acid mixture with a P2O5:SO3 ratio of 1:2.3.
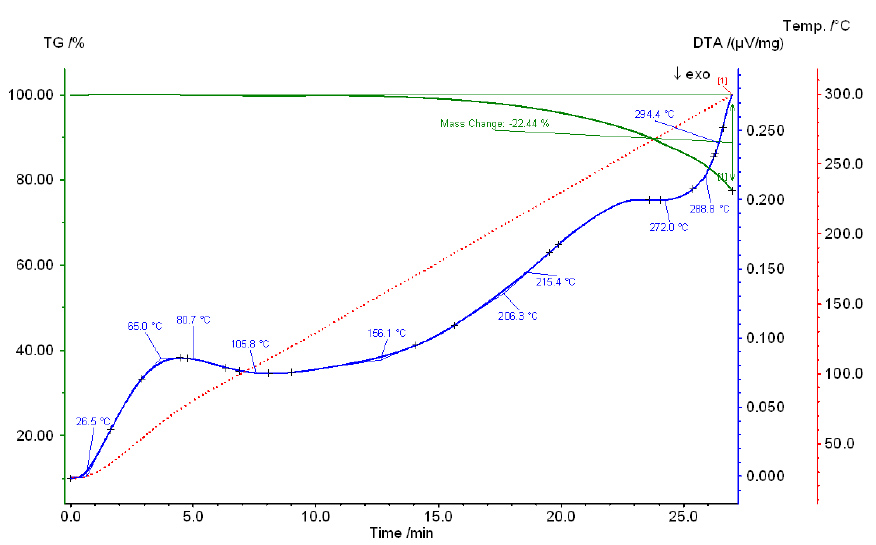
Thermogram of a phosphoric and sulfuric acid mixture with a P2O5:SO3 ratio of 1:4.4.
The content of SO3 in the mixtures remains almost unchanged in the temperature range from 100 to 250°C, with only a slight loss of SO3 observed at 300°C. In this temperature range, no loss of P2O5 occurs.
Thus, as demonstrated by the chemical analysis of the initial mixtures and heating products, the dehydration of phosphoric acid in the presence of sulfuric acid differs from that of pure phosphoric acid. While dehydration of orthophosphoric acid results in P2O5 loss and the formation of polyphosphoric acids starting from 220°C and above, no loss of P2O5 is observed at the same temperature for phosphoric acid in the presence of sulfuric acid at the specified SO3 content. At 300°C, only pyroform appears, and its content decreases as the amount of SO3 increases.
Heating of pure phosphoric and sulfuric acids is accompanied by significant endothermic effects, which shift to higher temperatures as the acid concentration increases. The results of thermographic analysis of pure phosphoric and sulfuric acids, along with their mixtures, over 4 hours are illustrated in Figs. 3-7.
Thermograms of all studied mixtures exhibit two endothermic effects, which likely correspond to the boiling points of phosphoric acid and sulfuric acid. The boiling point of pure H3PO4 is 261°C, while that of 98.3% H2SO4 is 338°C. Notably, the effect associated with the boiling point of phosphoric acid shifts to higher temperatures as the sulfuric acid concentration in the mixture increases. For example, in mixture I (36.79% SO3), this effect occurs at 240°C, while in mixture IV (55.90% SO3), it occurs at 280°C. Similarly, the effect associated with the boiling point of sulfuric acid also shifts to higher temperatures as the P2O5 content increases in the mixture: for mixture I (38.34% P2O5), it occurs at 375°C, and for mixture IV (22.20% P2O5), it occurs at 350°C.
The results of the chemical analysis of the heated mixtures over 4 hours, along with the data on their weight loss, indicate that as the temperature increases, the total weight loss increases for all mixtures in a similar manner. This is further supported by the curves' progression.
The IR spectra for the system tributyl phosphate (hereafter referred to as TBP) - H3PO4 - H2O are illustrated in Fig. (8), with the frequencies of the absorption band maxima listed in Table 4.
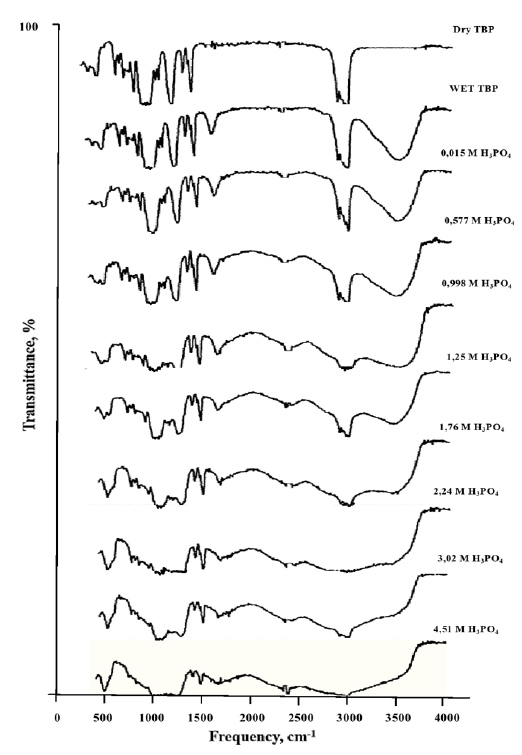
IR spectra of the extracts in the TBP - H3PO4 - H2O system.
No. | 1 | 2 | 3 | 4 | 5 | 6 | 7 | 8 | 9 | 10 |
---|---|---|---|---|---|---|---|---|---|---|
ν, Α<−1 |
552 | 428 | 464 | 488 | 488 | 492 | 492 | 484 | 488 | 484 |
595 | 464 | 536 | 536 | 536 | 536 | - | - | - | - | |
887 | 552 | 736 | 612 | - | 736 | 736 | 736 | 736 | 736 | |
937 | 612 | 768 | 736 | - | 772 | 768 | 772 | 772 | - | |
975 | 736 | 812 | 772 | - | 808 | 812 | 812 | 808 | 812 | |
1025 | 808 | 864 | 812 | 812 | 912 | 912 | 908 | 912 | - | |
1137 | 908 | 912 | 912 | 912 | 988-1036 | 976-1052 | 956-1068 | 872-1048 | 968-1056 | |
1175 | 1024 | 1024 | 1024 | 1024 | - | - | - | - | - | |
- | 1120 | 1120 | 1120 | - | 1120 | 1120 | - | - | - | |
- | 1152 | 1152 | 1152 | - | 1152 | 1152 | - | - | 1204 | |
1275 | 1256 | 1264 | 1260 | 1242 | 1232 | 1228 | 1224 | 1220 | 1384 | |
1375 | 1384 | 1384 | 1384 | 1384 | 1384 | 1384 | 1384 | 1384 | 1468 | |
1487 | 1468 | 1468 | 1468 | 1468 | 1468 | 1468 | 1468 | 1468 | 1648 | |
- | 1632 | 1636 | 1636 | 1636 | 1636 | 1636 | 1648 | 1644 | 2316 | |
- | 2324 | 2324 | 2324 | 2324 | 2328 | 2316-2392 | 2316-2404 | 2320-2384 | - | |
- | 2876 | 2876 | 2876 | 2876 | 2872 | 2868-2952 | 2876 | 2872 | 2960 | |
2975 | 2960 | 2960 | 2960 | - | 2960 | - | - | 2960 | - | |
- | 3468 | 3428 | 3424 | 3420 | 3412 | - | - | - |
According to the literature, pendulum vibrations around 720 cm−1 are commonly observed in structures containing chains with more than four CH2 groups. Therefore, the band at 736 cm−1 likely corresponds to CH2 group vibrations. The valence (stretching) vibrations of CH2 groups typically appear in the 3049–3018 cm−1 range. Bands in the 900–1100 cm−1 region are attributed to C–C stretching vibrations, while those between 1155–1200 cm−1 are associated with C–O bonds. Deformation (bending) vibrations of CH2 groups are generally observed near 1468 cm−1. Additionally, two bending vibrations are characteristic of methyl groups: the symmetric deformation (δₛCH3) at approximately 1375 cm−1 and the asymmetric deformation (δACH3) at around 1450 cm−1.
The methyl groups exhibit two distinct bands at 2962 cm−1 and 2972 cm−1. The first band results from asymmetric valence vibrations, where two C-H bonds in the methyl group are stretched while the third is compressed (UavCH3). The second band corresponds to symmetric valence vibrations (VSCH3). The presence of multiple groups in the molecule leads to strong absorption at these frequencies. In the systems studied, a strong absorption band appears in all spectra at 2960 cm−1. Weak bands in the range of 410–1170 cm−1 may correspond to vibrations of the free tetrahedral PO43− ion. Table 5 presents the areas of manifestation of internal (valence and strain) vibrations of the orthophosphate ion PO43− [43].
H2PO4− | HPO42− | PO43− | |||
---|---|---|---|---|---|
Wave number ranges, cm−1 | Description of oscillations | Wave number ranges, cm−1 | Description of oscillations | Wave number ranges, cm−1 | Description of oscillations |
300-570 | δ(O2PO2) | 350-580 | δ(O3P) | 410-490 510-670 |
δs (PO4) δas(PO4) |
700-900 | γ (POH) | 700-900 | ν (POH) | - | - |
840-910 | νs (PO2(H2)) | - | - | - | - |
915-970 | νas (PO2 (H2)) | 860-915 | ν (PO(H)) | 930-990 | νs (PO4) |
1030-1090 | νs (PO2) | 1040-1170 | νas (PO3) | 975-1140 | νas (PO4) |
1220-1370 | δ(POH) | 1210-1400 | δ(POH) | - | - |
1580-1700 | - | 1400-1750 | - | - | - |
2350-2400 | - | 2300-2450 | - | - | - |
3250-2750 | ν (OH) | 3250-2600 | ν (OH) | - | - |
Spectrum No | 1 | 2 | 3 | 4 | 5 | 6 | 7 | 8 | 9 | 10 |
---|---|---|---|---|---|---|---|---|---|---|
(H3PO4) water,mol/l | 0 | 0 | 1,03 | 2,49 | 3,78 | 4,42 | 5,88 | 7,69 | 10,22 | 12,60 |
(H3PO4) org,mol/l | 0 | 0 | 0,150 | 0,577 | 0,998 | 1,25 | 1,76 | 2,24 | 3,02 | 4,51 |
ν P=O, cм−1 | 1275 | 1256 | 1264 | 1260 | 1242 | 1232 | 1228 | 1224 | 1220 | 1204 |
ν OH, cм−1 | 3468 | 3428 | 3424 | 3420 | 3412 | - | - | - | - | |
∆ν P=O, cм−1 | - | - | −8 | −4 | 14 | 24 | 28 | 32 | 36 | 52 |
∆ν OH, cм−1 | - | - | 40 | 44 | 48 | 56 | - | - | - | - |
Spectrum No. | bond | ||||
---|---|---|---|---|---|
1 | 2 | 3 | 4 | 5 | |
ν, (cм−1) | |||||
492 | 396 | 364 | 348 | 392 | - |
608-648 | 592-708 | 592-652 | 596-648 | 496-616 | C-C (def.) |
816 | 816 | - | - | - | - |
940 | 940 | 948 | - | - | - |
1040 | 1040 | 1040 | 1040 | 1024 | C-O (val.) |
1112 | 1112 | 1116 | 1116 | 1164 | C-C (val.) |
1172 | 1244 | 1168 | 1176 | - | - |
1244 | 1388 | 1244 | 1244 | - | C-O (val.) |
1388 | 1468 | 1376 | 1392 | 1392 | - |
1468 | 1652 | 1468 | 1468 | 1468 | C-H (def.) |
2956 | 1648 | 1644 | 1640 | O-H (def.) | |
2956 | 3376 | 2956 | 2956 | 2956 | C-H (val.) |
3340 | - | 3360 | 3348-3408 | 3332-3404 | O-H (con.) |
The band at 1268 cm−1 in the spectrum of dry TBP [44] is attributed to the vibrations of the phosphoryl group P=O, while the band at 1040 cm−1 corresponds to the vibrations of the single P-O bond. Absorbance in the region of 910–1040 cm−1 is attributed to P-OH vibrations, and the band at 2324 cm−1 corresponds to the P-H bond. As the acid concentration in the extracts increases, a shift of the absorption band maxima for the P=O and OH bonds toward lower frequencies is observed, indicating the interaction of the phosphoryl group with water and the formation of hydrogen bonds. Spectral analysis shows that after contact between the extractant and water (spectrum 2), two new bands appear in the region of 1600–1800 cm−1, related to the deformation vibration of bound water, and another band in the region of 3400–3500 cm−1, caused by the valence vibrations of free (unbound) water molecules. According to previous studies [45, 46], the bands near 1700 cm−1 are attributed to the deformation vibrations of the hydrated proton H3O+, while the broad intensity bands in the region of 2300–2800 cm−1 correspond to the valence vibrations of O-H bonds in these groupings. As the acid concentration in the extracts increases, a shift in the maxima of the absorption bands for the P=O and OH bonds toward lower frequencies is observed, indicating the interaction of the phosphoryl group with water and the formation of hydrogen bonding.
The distribution of water in phosphorus-containing compounds was studied, and the existence of the compound TBP*H2O was proposed (Table 6).
It is known that during the extraction of mineral acids, the proton of the acid binds to the oxygen atom of water, forming a hydroxonium ion (H3O+), which is subsequently hydrated by several water molecules. The hydroxonium ion typically exhibits a spectral band near 1700 cm−1 [47, 48]. However, this band is absent in our spectra. The absence of this absorption band suggests that, during extraction with tributyl phosphate, phosphoric acid remains in its undissociated form within the organic phase.
During the extraction of phosphoric acid with tributyl phosphate, increasing the acid concentration (up to 2.24 mol/L) leads to a decrease in the intensity of the bands associated with the phosphoryl group. As the concentration increases further, the bands corresponding to water vibrations disappear. This can be explained by the formation of a hydrate-solvate complex during extraction from dilute phosphoric acid solutions, where water is abundant. In such cases, water molecules are incorporated into the extracted complex along with tributyl phosphate. However, as the acid concentration rises, the activity of water in the aqueous phase decreases, reducing the hydration of the extracted complex. At higher concentrations, the complex becomes dehydrated, resulting in the disappearance of water-related bands in the spectra.
In contrast, no significant spectral changes are observed in the system with n-butyl alcohol (Table 7 and Fig. (9), indicating that extraction occurs via a physical distribution mechanism. Based on physicochemical measurements, it can be concluded that alcohols extract phosphoric acid through physical distribution, while tributyl phosphate operates via a hydrate-solvate extraction mechanism.
In the next series of experiments, the dehydration of phosphoric acid in the presence of sulfuric acid, with P2O5:SO3 ratios of 1:1 and 1:1.7, was studied as a function of heating duration at 250°C.
Experimental results showed that the dehydration of phosphoric acid was significantly affected by the heating duration. After 4 hours of heating, the acid remained in the orthoform. By 10 hours, the SO3 content increased, and after 150–160 hours, high-molecular-weight polyforms were formed, with a total P2O5 content of 78.84%–80.00% and SO3 content of 2.35%–2.30%. When stored for 1–2 months in a desiccator over P2O5, these dehydrated products developed into long, thin, crossed druse needles. Acids with 78.84% P2O5 and 2.30% SO3 were crystallized completely upon mechanical agitation with a glass rod.
The total weight loss depends on both the heating time and the SO3 content of the mixtures. After 15 hours of heating, the weight loss was 50.6%. With further heating up to 150-160 hours, the weight loss changed very little, only increasing by 0.76%. As heating time increased, SO3 was lost (95%–97%), along with a loss of P2O5 (4.59%–11.65%). When SO3 was removed from the mixture, the total losses remained small, and the condensation process became very slow, similar to pure phosphoric acid. To extend the dehydration duration, the heating temperature of the mixture was increased to 400°C. Experiments were conducted with mixtures at 1:1.7 and 1:4.4 ratios, which were heated until SO3 release ceased (3 hours). The results of the chemical analysis indicated that SO3 was completely absent in the products, and the total P2O5 content was 86.88%–87.41%, which did not depend on the initial composition of the mixture. The content of polyforms in the products was 83%–89.3% of the total phosphorus pentoxide.
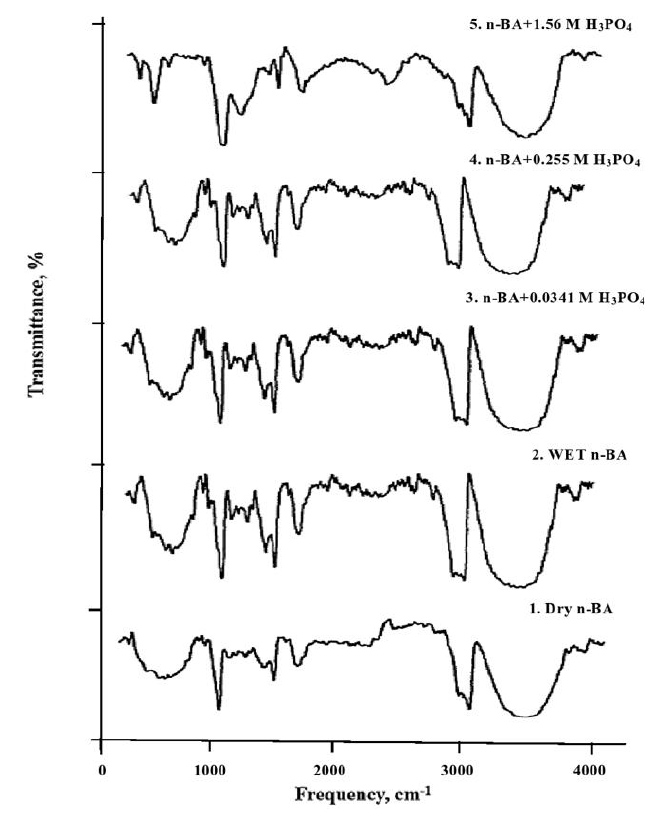
IR spectra of extracts in the system n-BA - H3PO4 - H20.
The dehydrated products showed the presence of all condensed forms of phosphoric acid, which are consistent with those found in the dehydration product of orthophosphoric acid.
Thus, the dehydration of phosphoric acid in the presence of sulfuric acid depends on both the temperature and duration of the process, as well as the amount of sulfuric acid in the mixture.
CONCLUSION
The findings of this study make a significant contribution to optimizing phosphoric acid extraction using organic solvents. The selected solvents enabled the production of a high-P2O5-content product (56%–63%), with n-butanol yielding a purer final product compared to previously studied solvents—marking a notable advancement in commercial phosphoric acid purification.
A key innovation of this work is the detailed analysis of extraction mechanisms using different solvents, including n-butanol, tributyl phosphate, and isoamyl alcohol. Unlike conventional alcohols that extract phosphoric acid via physical distribution, n-butanol operates through a hydration–solvation mechanism. This makes it more effective, especially under conditions where other solvents show reduced efficiency. These insights deepen the scientific understanding of solvent-based extraction processes and open new pathways for enhancing phosphoric acid purification technologies.
The results of this work are directly applicable to industrial efforts aimed at developing more efficient and environmentally friendly methods for the technical purification of phosphoric acid, aligning with modern standards for product quality improvement. This approach significantly reduces contaminants such as sulfates and fluorides, allowing the purified phosphoric acid to be used in the production of high-quality phosphorus fertilizers. The uniqueness of this study lies in its integrated approach—combining strategic solvent selection with a comprehensive analysis of the physical and chemical properties of the solvents. Results showed that increasing the initial phosphoric acid concentration from 5.38% to 25.61% P2O5 at 25°C led to a corresponding increase in the distribution factor. However, increasing the temperature from 25°C to 60°C had minimal impact on the distribution factor, indicating that concentration plays a more critical role than temperature in the efficiency of extraction.
The distribution factor of sulfuric acid increases with its initial concentration when using n-butyl and isoamyl alcohols. The presence of magnesium sulfate in phosphoric acid, in amounts up to 1.05% MgO, has little to no effect on the distribution coefficient of phosphoric acid, whereas the presence of magnesium monophosphate reduces it by nearly half.
Phosphoric acid is more effectively extracted with n-butanol. Through azeotropic sublimation of the solvent, a relatively pure phosphoric acid product with a high phosphorus pentoxide content (56%–63%) is obtained. To determine the composition of the extractable complexes during phosphoric acid extraction with tributyl phosphate and n-butyl alcohol, IR spectroscopic studies were conducted on extracts from the TBP–H3PO4–H2O and n-BA–H3PO4–H2O systems. The physicochemical measurements indicate that alcohols extract phosphoric acid through a physical distribution mechanism, whereas tributyl phosphate operates via a hydrate–solvate extraction mechanism.
The dehydration of phosphoric acid in the presence of sulfuric acid was studied as a function of sulfuric acid content, temperature, and duration of the dehydration process. At 250°C, no polyforms of phosphoric acid were formed, and there was no loss of P2 O5 or SO3. At 300°C, polyform formation still did not occur, and the presence of SO3 in the mixture further suppressed polyform development. However, at 400°C, complete removal of SO3 was observed. Prolonged heating (160–200 hours) of phosphoric and sulfuric acid mixtures at 250°C resulted in the near-complete removal of SO3 (95%–97%) and the formation of polyphosphoric acids. These research findings can be applied to the development of a basic technological scheme for the deep purification of technical-grade phosphoric acid, enabling the production of highly concentrated phosphoric acid containing no more than 0.002% residual sulfuric acid impurities.
AUTHORS’ CONTRIBUTIONS
The authors confirm their contributions to the paper as follows: Analysis and interpretation of results – L.K.; draft manuscript – S.A., M.S., and G.K.; investigation: S.A.; visualization: AB. All authors reviewed the results and approved the final version of the manuscript.
LIST OF ABBREVIATIONS
n-BA | = n-Butyl alcohol |
TBP | = Tributyl phosphate |
AVAILABILITY OF DATA AND MATERIALS
The data and supporting information are available within the article.
ACKNOWLEDGEMENTS
Declared none.