All published articles of this journal are available on ScienceDirect.
Mechanical and Structural Properties of Epoxy Resin-Allyl Guar Gum Composites
Abstract
Introduction:
Guar gum is a non-ionic polysaccharide extracted from the endosperm of Cyamopsistetragonalobus. Guar gum and its derivatives are water-soluble hydrophilic polysaccharides, and hydrophobic modification is required to increase its compatibility in a polymer matrix.
Objectives:
The present study investigates the synthesis of allyl-modified guar gum (AGG) and epoxy resin composites. The mechanical properties of the prepared composites with varying concentrations of filler (allyl guar gum) in the range of 0.5-4.5 wt% have been evaluated. The mechanical and structural properties of the prepared composites have been investigated using Universal Testing Machine (UTM) and Scanning Electron Microscope (SEM), respectively.
Methods:
The epoxy composites were prepared by casting technique using allyl guar gum as the filler. The polymer-filler interactions varied with the contents of the filler.
Results:
The tensile strength was found to be enhanced up to 13% at 0.5% concentration of AGG. The % elongation at break values followed an opposite trend as compared to the tensile strength data of the composites. The observed mechanical properties have been correlated with the fracture morphology of the composites.
Conclusion:
A better dispersion, that is, polymer-filler interactions, improved the tensile strength of composites, while poor interactions declined the tensile strength. It is reported that max tensile strength can be obtained at 0.5% concentration of allyl guar gum (AGG1). The maximum increase in % elongation at break was 25% for AGG2-based epoxy composite at 3% of filler concentration.
1. INTRODUCTION
Plastics made from petroleum are widely used throughout the world for numerous applications. On the other hand, the disposal of waste plastic has become a serious environmental threat. Therefore, the development of novel plastic that could be degraded by indigenous microorganisms present in soil and water systems has recently attracted much attention. In this regard, biodegradable materials have been paid attention to as an alternative to petroleum-derived plastics [1]. A variety of natural biopolymers, including starch, cellulose, and chitosan, have been tested alone or combined with synthetic polymers for the possibility to develop fully or partially biodegradable films. Guar gum is the endosperm polysaccharide of the seed of Cyamopsis tetragonolobus [2]. It is a galactomannan consisting of backbones of α-1,4 D mannopyranosyl with every second unit bearing a β 1,6D–galactopyranosyl unit [3]. It is easily available and cheap in many parts of the world. India is the largest exporter of guar gum. Guar gum is extremely hydrophilic and water-soluble. The hydrophilic nature of guar gum hampers its interactions with the hydrophobic polymer matrix [4, 5]. Hydrophobic modification of guar gum is required to increase its compatibility with polymers. This integration has allowed these polymers and their derivatives to be commercialized in diverse fields, such as textiles, foods, cosmetics, pharmaceuticals, binders for electrodes and separators, and corrosion inhibition of iron-gall ink in paper works [6-10].
Epoxy resins are important thermosetting polymers and have a good combination of important properties, like excellent insulation, volatile less-flexible curing systems, and moisture resistance; epoxy resins are widely used as matrix resin in composites and as structural adhesives due to their remarkable bonding ability to various materials, including metals, ceramics, wood, and plastics [11].
The guar gum has been modified to prepare acryloyl, acetylated, and methacryloyl derivates of guar gum [12-14]. However, limited studies are available on the allyl etherification of guar gum. In a previous study [4], allyl guar gum was prepared by reaction of guar gum with allylchloride to effect etherification and it was characterized by FTIR, TGA, and SEM analyses. The different degree of substitution of AGG was realized by varying the concentration of sodium hydroxide and allyl chloride to guar gum (Table 1). The free hydroxyl groups along the polysaccharide backbone of guar gum were substituted by allyl groups to improve the hydrophobicity and inhibit aggregation in an aqueous environment. In this study, the composites of epoxy resin with different % of allyl-modified guar gum as fillers have been prepared. The mechanical properties of these composites have been investigated. The fracture morphology of these composites has been recorded to decipher the observed mechanical properties.
Sample name | Volume of NaOH | Wt of allyl chloride | Temperature (oC) | Time (hrs) | DS |
---|---|---|---|---|---|
AGG1 | 7 | 6.84 | 50 | 4 | 0.0389 |
AGG2 | 7 | 6.84 | 50 | 8 | 0.0625 |
2. MATERIALS AND METHODS
The epoxy composites were prepared by casting technique using allyl guar gum as the fillers. Epoxy resin (DGEBA) was purchased from Dow Chemicals. The allyl-modified guar gum was prepared as reported previously [15]. The degree of substitution of allyl guar gum was calculated by titration method [16]. A typical chemical structure of allyl guar gum (AGG) is shown in Fig. (1). The fillers were dispersed in the epoxy resin in different wt% of 0.5 to 4.5. Polyetheramine D230 was added as a curing agent and the composite was mixed thoroughly. The formulation was then de-aerated and poured into a preheated metal mold at 60 °C. The cure cycle adopted for the preparation of the epoxy composites was 60 °C for 4 h. The thickness of the prepared composites was found to be 3 mm. The composites were cut into the respective shapes for testing and the edges were uniformly ground to remove imperfections.
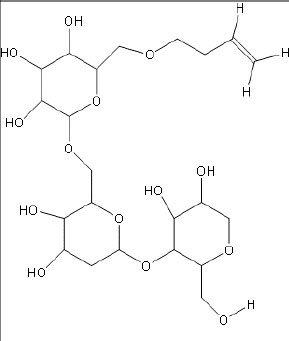
2.1. Characterization of the Prepared Composites
The morphology of the composite samples was investigated using scanning electron microscope (HITACHI S 3700N) at a voltage of 15KV. The samples were coated with gold for this analysis [17]. The mechanical properties (tensile strength, % elongation at break) of the prepared composites were analyzed using the universal testing machine (Instron 3369) with a crosshead speed of 5 mm/min. The dimensions of the specimen were 10 cm × 1 cm with a gauge length of 3.0 cm. The tensile strength was evaluated as per ASTM D638. The impact strength of the composites was measured using the Izod impact strength according to ASTM D790 at a crosshead speed of 2 mm/min.
3. RESULTS AND DISCUSSION
3.1. Mechanical Properties of the Synthesized Epoxy Allyl Guar Gum Composites
The tensile strength, elongation at break (%), and impact strength of the prepared epoxy composites with varying contents of two allyl guar gums (AGG1 and AGG2) are shown in Fig. (2). The tensile strength of the epoxy composites was found to increase at 0.5% concentrations of AGG1 and AGG2, and further addition resulted in a declining trend (Fig. 2A). The tensile strength was enhanced by 13 and 8% in the case of AGG1 and AGG2-based composites, respectively. This decrease at higher filler concentration could be due to the presence of double bonds. The increase in tensile strength at lower concentration may be due to the reinforcing action of the fillers. Better filler-polymer interactions improved the tensile strength and decreased elongation at break values [18]. A lower value of tensile strength of the AGG2 epoxy composites at the same concentration of filler as compared to AGG1-based composites indicated that the higher degree of substitution hindered the filler-polymer interactions. The decrease in the tensile strength was observed at filler concentrations above 0.5% due to poor interactions and phase separation. The impact properties of composites also followed a similar trend as tensile strength, as shown in Fig. (2). The impact strengths on the addition of AGG1 were greater than that of AGG2 concentration on the basis of increased interactions of epoxy resin. The maximum value of impact strength was observed at 1.5% of filler concentrations, which may be due to greater interaction resulting in composites with greater impact strength.
The % elongation at break of the composites displayed an initial decrease corresponding to the maximum value of tensile strength, as shown in Fig. (2b). There was a gradual increase in elongation at break values as the concentration of filler increased. The maximum elongation was observed at 3% of filler concentrations (Fig. 2b). The % elongation at break values followed the reverse trend as compared to tensile and impact strength data, that is, better elongation was observed in AGG2 composites than in AGG1 at the same filler concentrations. The maximum increase in % elongation at break was 25% for AGG2-based epoxy composite at 3% of filler concentration. A further increase in filler concentrations above 3% resulted in a decrease of % elongation at break. However, % elongation at break was still greater than that of neat epoxy resin.
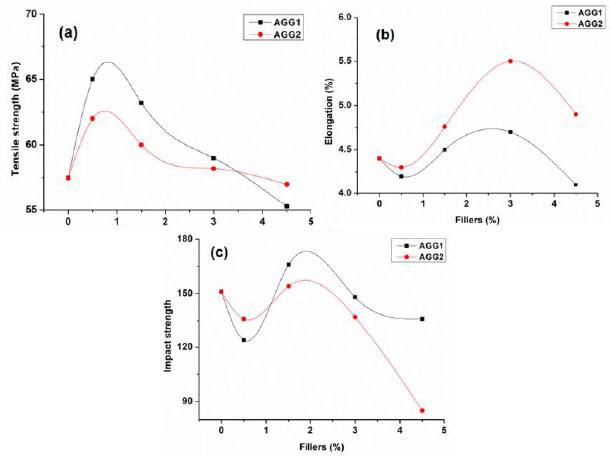
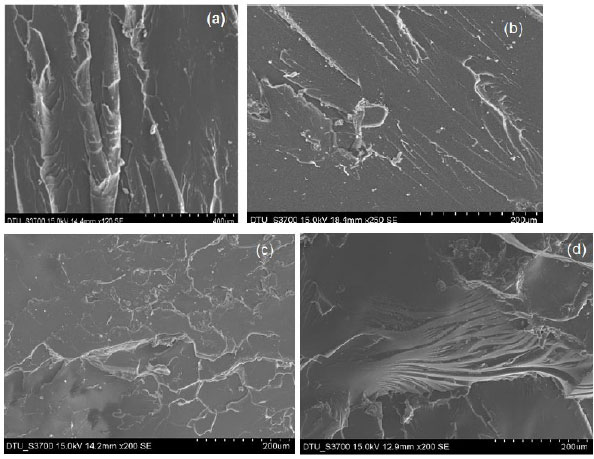
3.2. Fracture Morphology of the Prepared Composites
The fracture morphology of neat epoxy resin and composites is shown in Fig. (3). The composites filled with low allyl guar gum showed an increase in matrix region as compared to composites with higher contents of allyl guar gum. The micrograph observed for the unmodified formulation was characteristic of a brittle system having a smooth glassy fractured surface with cracks in different planes, while rough fracture surfaces were observed for the composites. A similar morphology of neat epoxy resin was reported [9]. The composites containing 1.5% of AGG1 and AGG2 exhibited good dispersion of both phases and a lower extent of unreacted polymer (Fig. 3b-d). This resulted in improved tensile strength and impact strength [11]. The fracture path of AGG1 showed a large breadth and parallel fibril structure, which indicated the stretching prior to fracture (Fig. 3b). The formation of agglomerates was seen in the case of AGG2 due to reduced filler-polymer interaction [19-22] (Fig. 3c). Therefore, composites with 0.5% of AGG1 resulted in higher tensile strength than the same contents of AGG2. A further increase in the content of modified guar gum resulted in poor dispersion of two phases. The extent of unreacted DGEBA and modified guar gum is shown by major black and white spots in the micrograph (Fig. 3d), respectively. However, the fracture path of AGG2 was very narrow, and continuous rapid propagation along the axis of crack growth was observed (Fig. 3d).
CONCLUSION
In the present study, allyl-modified guar gums (AGGs) were composited with epoxy resin. The AGG with two different degrees of substitutions was used. The polymer-filler interactions varied with the contents of filler (AGG) and degree of allyl substitutions, which in turn affected the mechanical properties of the composites. The mechanical properties of the composites showed a dual behavior depending on the contents of the filler. The tensile strength of the composites was found to be enhanced by 13% at a 0.5% concentration of AGG1 as compared to neat epoxy resin. The % elongation data exhibited an opposite trend as compared to the tensile strength of the composites. The maximum increase in % elongation at break was 25% for AGG2-based epoxy composite at 3% of filler concentration. The altered mechanical properties of the composites correlated with the dispersion of filler in the polymer matrix and phase separation.
LIST OF ABBREVIATIONS
AGG | = Allyl Guar Gum |
UTM | = Universal Testing Machine |
SEM | = Scanning Electron Microscope |
AUTHOR’S CONTRIBUTIONS
Dr. Gopal Arora is thankful to Chancellor, Dr. Sachin Gupta, Sanskriti University, Mathura, Dr. D S Tomar (Dean & HOD), and Sh Pooran Singh (Registrar), for help and support. Dr. Gopal Arora also thanks Mr. G.G. Kuswaha, Dr. Devender Kr Verma, Mr. B.K. Sharma, and Jeevan Ram for their valuable help during the work.
CONSENT FOR PUBLICATION
Not applicable.
AVAILABILITY OF DATA AND MATERIALS
The data supporting the findings of the article is available in the reference number [13].
FUNDING
None.
CONFLICT OF INTEREST
The authors declare no conflict of interest, financial or otherwise.
ACKNOWLEDGEMENTS
Declared none.